Videos
Loading the player ...
- Offer Profile
SOLUTIONS THAT MOVE
Burgstetten near Stuttgart is home to BINDER GmbH, an owner-managed family company run by two generations of the Binder family. Since its foundation in 1971 BINDER has been designing and implementing innovative and customer-centric solutions in material handling.
45 years of experience, modern machinery and a wide range of services – this is what makes up BINDER. Our knowledge, experience and vision allow us to meet our customers as partners and to support them during the entire project. Reliability, punctuality and high-quality implementation are the guiding principles which are at the bottom of our success as a company. Our effective company structure and motivated staff provide us with the necessary flexibility to meet our customers‘ demands.
Product Portfolio
PALLET CONVEYING
OUR SPECIALTY
We are an established partner for high-end integrated solutions. We are also
happy to implement small and medium-sized installations as system supplier.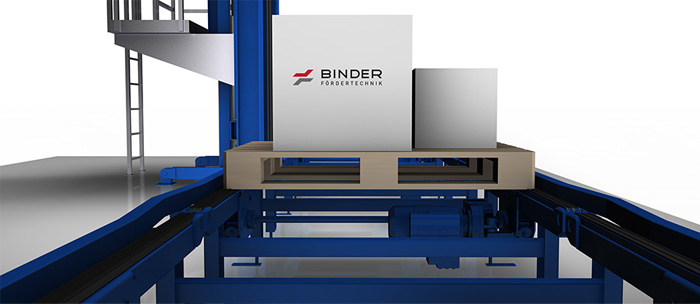
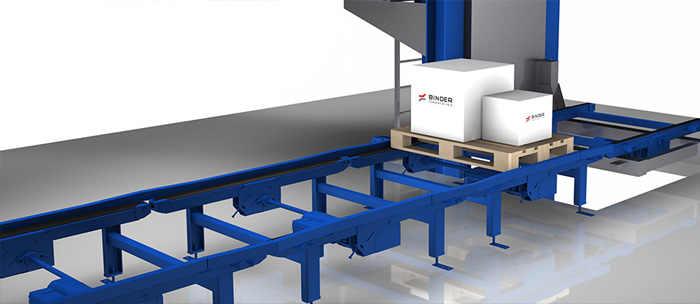
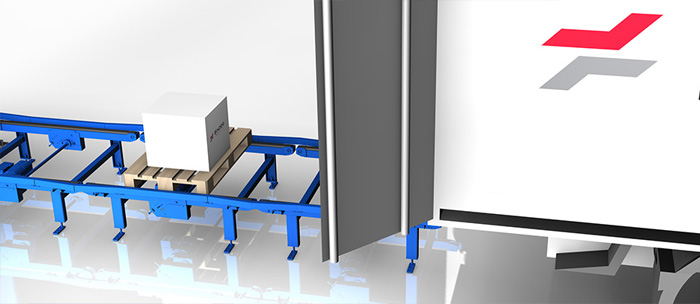
CHAIN CONVEYOR
- A roller chain bears the weight of the material for
conveying. The highly wear-resistant plastic slide rail attached to the
frame structure guarantees low-friction, low-noise running. The conveyor is
driven by a continuous shaft with a geared motor. The individual sections of
the chain are tensioned separately. Reversing operation is possible. Small
chain deflectors on roller bearings allow common loading aids to be
transported longitudinally or transversely without changing track. Grouping
is effected by clocked operation or bunching of the material for conveying.
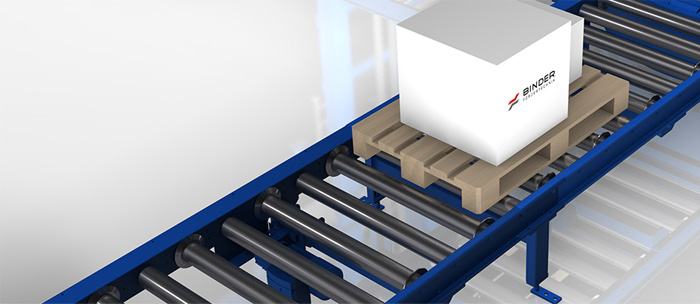
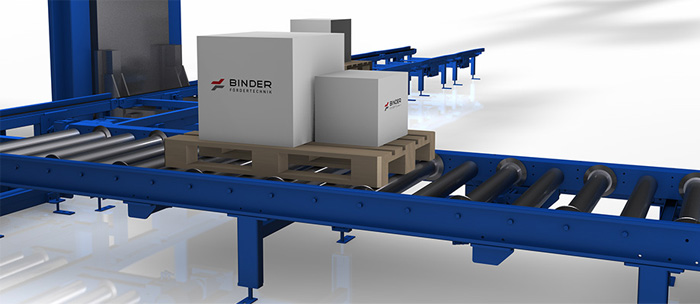
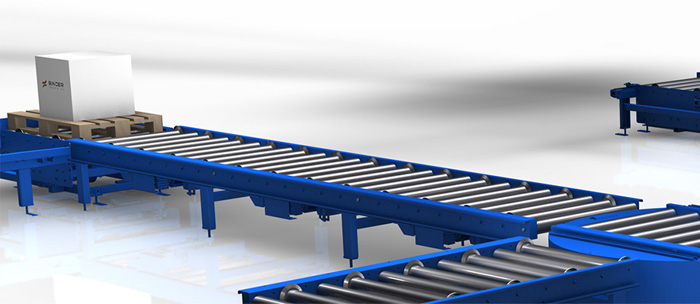
ROLLER BED
- The conveyor rollers are driven from roller to roller or
tangentially, with the drive and chain tensioning usually arranged in the
centre. Reversing operation is possible. The material for transport is
guided by flanges welded or clamped onto the rollers. Conveying is
continuous, the material for transport can be grouped by the control unit by
means of increasing clocking or bunching. Special designs in accordance with
individual customer requirements.
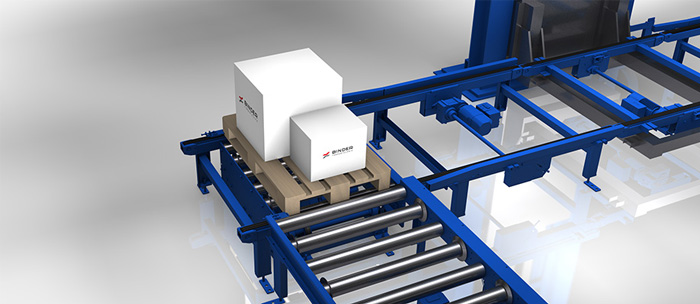
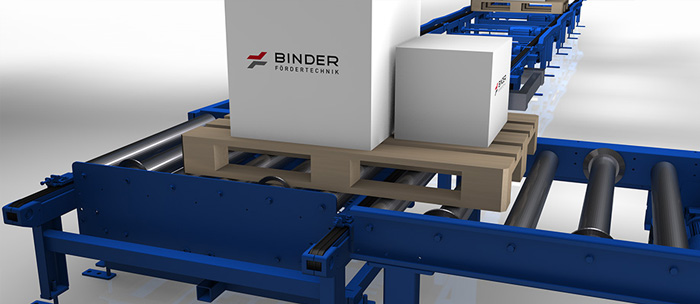
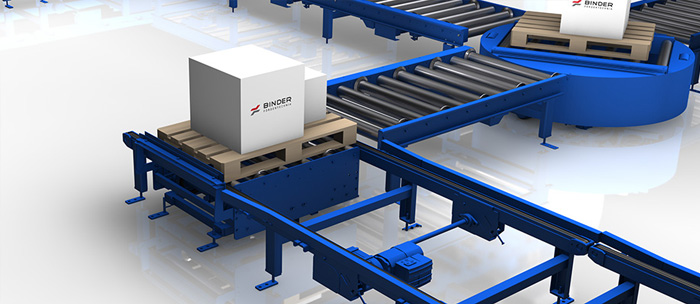
ANGULAR TRANSFER UNIT
- Lifting elements are fitted in the conveyor systems to
load and retrieve products at right angles to the direction of travel and to
transfer them between conveyor lines running in parallel. The lifting
movement is executed electromechanically using eccentric lifting shafts.
Axial rollers guide lifting precisely.
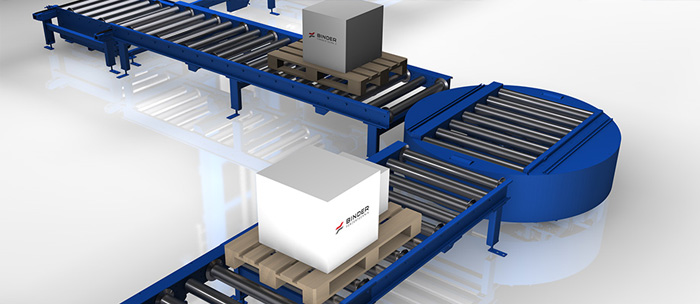
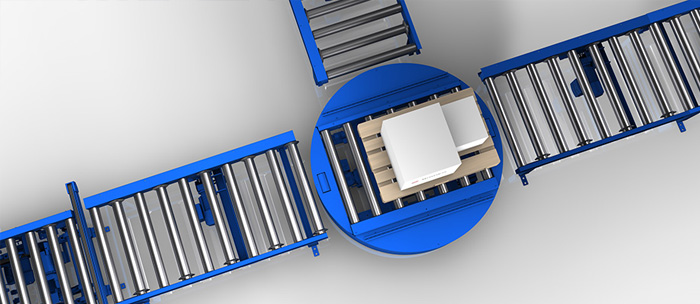
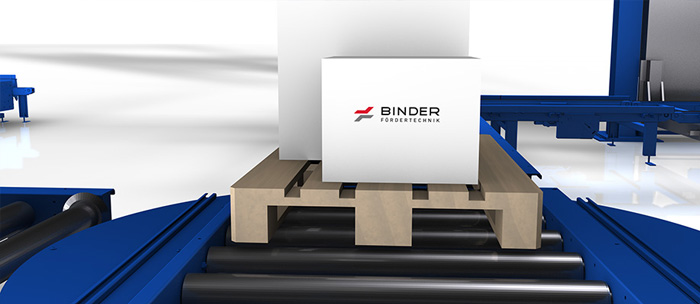
TURNTABLE & TILTING TABLE
- The turntables and tilting tables with chain conveyors or
roller beds mounted on top can swivel up to 360°; they are fitted in
conveyor systems at intersections and to effect a change in direction. Both
horizontal and vertical movements can be integrated to suit customer
requirements. The turning element is a high-quality single-row ball bearing
slewing ring with external gear.
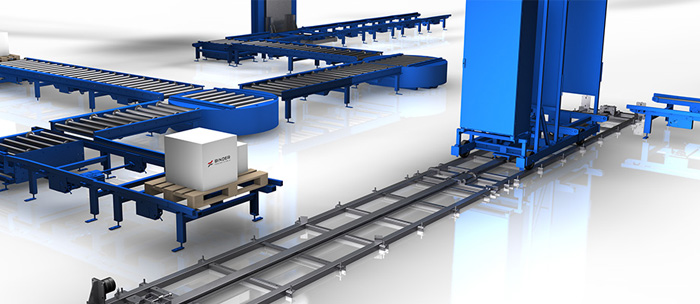
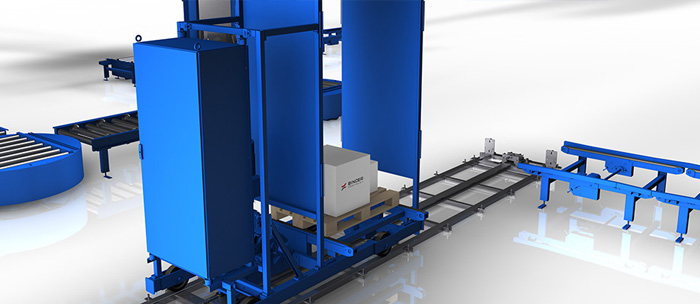

TRANSFER CAR
- Transfer cars are used for supplying and emptying spurs,
for picking stations and pallet stations and for connecting conveying
sections arranged offset from one another. The basic design consists of a
welded frame with an integrated chassis. Travelling movement is achieved
essentially by means of direct-driven wheels or toothed belts. When driven
by toothed belts, the motor can be arranged either stationary or travelling
on the car. Directional stability is ensured by adjustable guide rollers on
the sides. The Vulkollan wheels have very smooth-running and shock-absorbing
characteristics. It is possible to mount a variety of components on top for
transferring and forwarding the material for transport, such as chain
conveyors, roller beds or telescopic tables.
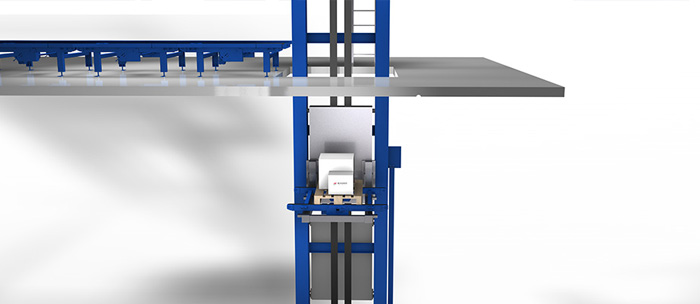
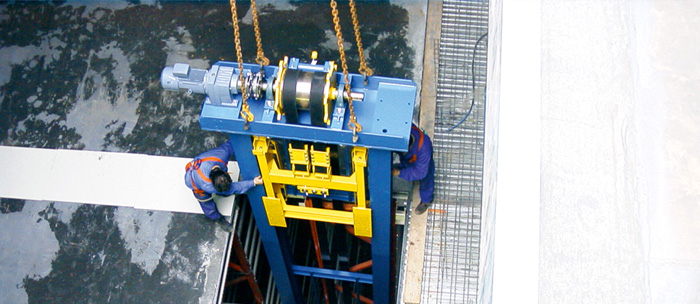
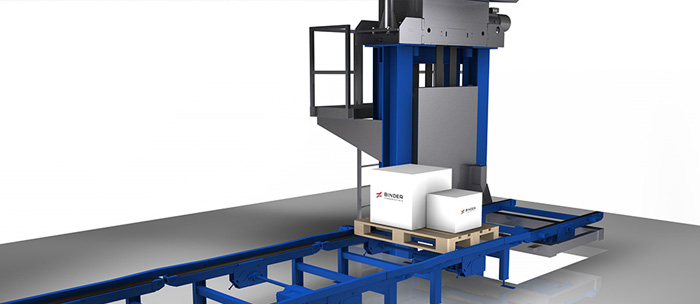
VERTICAL CONVEYOR
- VERTICAL CONVEYOR
Vertical conveyors are used to connect conveyor systems on different levels.
The lifting drive is provided by an electric motor, with flat belts, toothed
belts, cables or chains being used as carrier media. Depending on
requirements, 2-column or 4-column designs with the drive above or below can
be used. The type of conveyor mounted on the lifting carriage can be
realized to suit the individual application – in the form of a telescopic
fork, chain conveyor, roller bed, turntable or angular transfer unit.
CARRIER PLATE CONVEYING
- SPECIFICALLY FOR METAL CARRIER PLATES
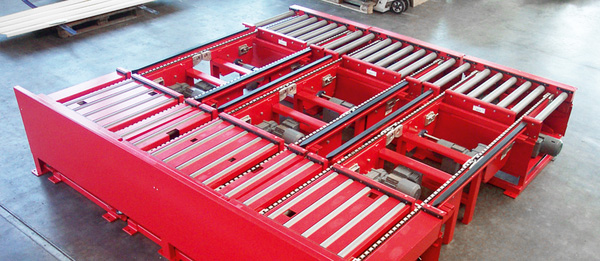
CARRIER PLATE CONVEYING
- Chain conveyors and roller conveyors with plastic
coatings ensure gentle and low-noise transport of metal carrier plates of
various sizes with total weights of up to 300 kg.
MODULAR BELT CONVEYING
- CAN BE USED FOR DIFFERENT LOADING AIDS
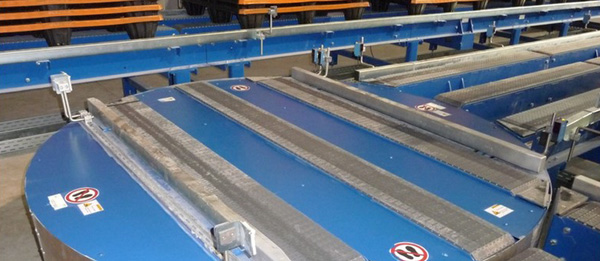
MODULAR BELT CONVEYING
- Modular belt conveyors are used for the continuous
transport of pallets and load carriers of various sizes.
DOLLY CONVEYING
- FLEXIBLE & SAFE CONVEYING
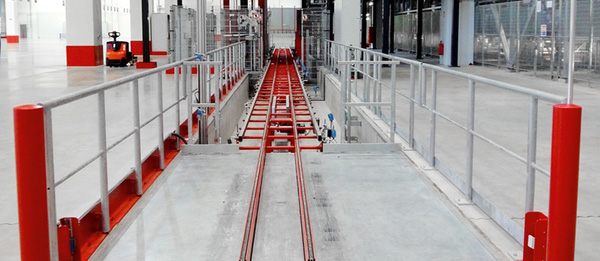
DOLLY CONVEYING
- Chain conveyors or belt conveyors safely transport
rolling containers of various sizes. Combined transport of rolling
containers and pallets is also possible.
SPECIAL SOLUTIONS
- INDIVIDUAL & CHALLENGING
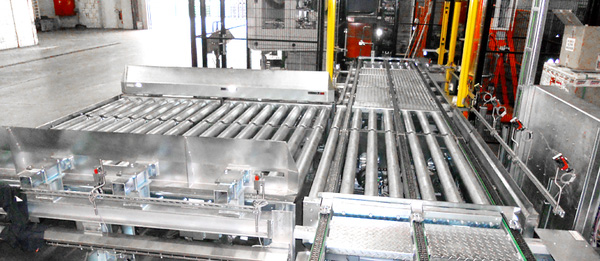
SPECIAL SOLUTIONS
- In addition to individual solutions we offer special
solutions, both integrated into complete systems and as separate elements
for new and existing installations.
Services
- CONVEYING IS A PROCESS:
AND WE ARE THE ONE-STOP PROVIDER TO SUPPORT IT
We are experts in providing special conveying solutions: covering
everything from project planning, in-house design and on-site manufacture to
assembly and commissioning at the location of use. Our portfolio also
includes upgrading and updating existing machinery and providing operator
training after successful commissioning. A staff of more than 50 skilled and
competent professionals with innovative ability guarantees our quality and
delivery reliability. PROJECT PLANNING
- YOUR REQUIREMENTS ARE OUR CHALLENGE
Different product requirements, local conditions and differences in
production processes require made-to-measure conveying solutions. At BINDER,
experienced professionals design for example storage and retrieval systems
for pallet high-bay racking, picking and dispatch areas and car body
transfer at the welding stage and for fi nal assembly. For this, various
types of loading equipment, such as pallets, rolling containers or carrier
plates are used. Our solutions make use both of tried and tested components
of unit load handling technology such as chain conveyors, roller conveyors
and modular belt conveyors, including any subassemblies required, and of
customised designs. MANUFACTURING
- QUALITY MANUFACTURING MADE BY BINDER:
WE WORK FOR YOUR SUCCESS
Our highly qualified and motivated staff and our modern machinery allow
us to manufacture virtually all the components needed in virtually any depth
of production. Our services also include contract manufacturing – based on
your drawings –, manufacturing of single pieces and the manufacture of
special-purpose machines, both for conveying and other equipment.
MACHINING
- CNC milling machines
- CNC automatic lathes
- Conventional lathes
- CNC drilling machine
- CNC saws
WELDING
- Welding robot
- Several welding machines for MIG, MAG und TIG welding
SHEET-METAL WORKING- Laser cutting plant
- Stroke scissors
- Mechanical press brakes
PAINTING
ASSEMBLY
- ASSEMBLY & SERVICE:
OUR SERVICES DO NOT STOP AT THE FACTORY GATES
Only ideally matched individual components will be shipped to the
customer. But we all know that the whole is more than the sum of its parts,
and therefore our conveyor systems are fine-tuned on site. Our customers
expect flawless installation and commissioning at their production sites,
after all. After going live we offer competent maintenance and a fast spare
parts service to ensure trouble-free operation. With our aftersales service
we will be your partner for the complete life cycle of your equipment.