JENOPTIK Industrial Metrology
Videos
Loading the player ...
- Offer Profile
- We are a globally operating technology group. Optical technologies are the very basis of our business with the majority of our products and services being provided to the photonics market.
Our key target markets primarily include the semiconductor equipment manufacturing and electronics industry, life science and medical technology, as well as traffic and the security industries.
In 2021, we generated revenue of 750.7 million euros in our continuing operations.
The Jenoptik Group is headquartered in Jena, Germany. In addition to several major sites in Germany Jenoptik is represented in Europe, in the USA, and Asia-Pacific. JENOPTIK AG is listed on the Frankfurt Stock Exchange and included in the SDax and TecDax indices.
Product Portfolio
Imaging Solutions and Cameras
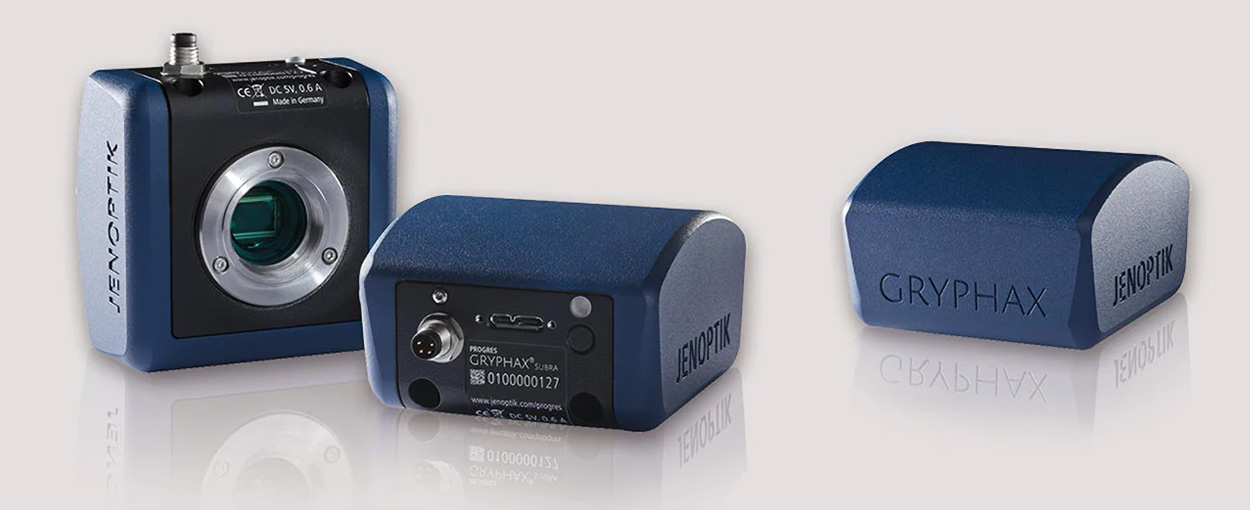
Imaging Solutions and Cameras – developed and produced individually for your diverse applications
Jenoptik delivers complex optoelectronic systems tailored to your applications. We do this by bundling our combined expertise in the areas of optoelectronic systems, optics, microoptics and sensors.
The experts at Jenoptik have been developing, constructing and producing powerful image processing solutions for over 25 years. Our professional digital cameras and camera modules are tried-and-tested across the globe. They guarantee outstanding image quality and accurate color representation. They are also supplied with our in-house company software and updates, which is compatible with all current operating systems and is very easy to operate. Our reliable and flexible products are therefore ideally suited to a wide range of metrology applications in the fields of science, research and industry.
As well as our proprietary microscope camera range, we also offer camera modules for your specific systems. All products are tailored perfectly to your areas of application. These include complete image processing systems, machines and devices. We do this by combining high-quality electronic system components with software for image processing, optics, lighting and mechanics.
You can also take advantage of our repair service, allowing you to send us faulty cameras or camera modules at any time. Our experts will assess them and provide you with a quote for the necessary repairs.
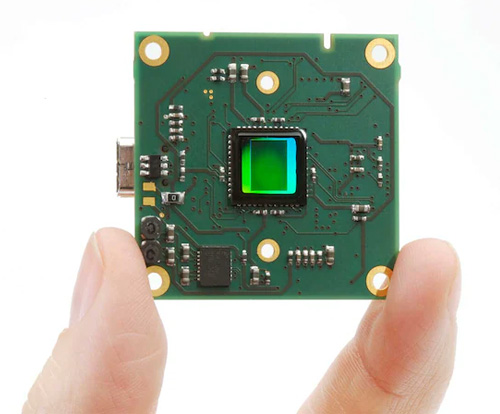
Customer-Specific Imaging Modules
- Jenoptik is a full-service provider that will develop your specific imaging concept for you — from the initial idea to the finished system.
Our high-performance cameras, image processing products and complete OEM systems are ideal for use in the scientific and industrial imaging market: We supply imaging modules both for high-volume projects and for individual projects.
We tailor all of our products to your precise requirements— with a complete value chain: from sensors and sensor boards through to camera system solutions with our own firmware for your specific application.
We optimize the basic version of our compact CMOS USB camera module for your needs. With a 5-megapixel resolution and a USB 2.0 interface, this module provides the ideal platform. We can deliver customer-specific modifications within a very short turnaround time. We can also make minor changes to the hardware and software or build complete systems from different modules for your image processing applications.
For more complex projects, we can combine the properties and features of our camera module according to your requirements.
They include:
- Form factor.
- Resolution (1 MP, 3 MP, 5 MP, 10 MP, 14 MP, ...).
- Sensor type (CCD / CMOS).
- Digital interface (USB 2.0, USB 3.0).
- Optical interface (C-mount, S-mount, CS-mount).
- Optics, filters and more.
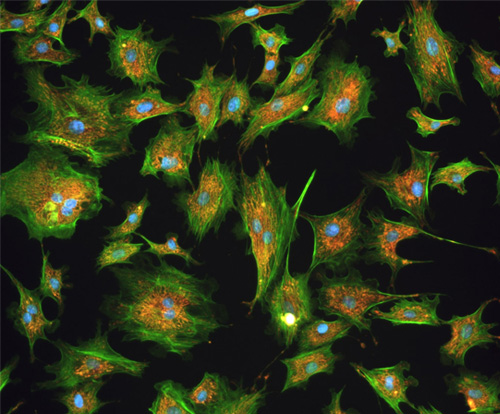
Miniaturized Digital Microscope Subsystem
- JENOPTIK SYIONS® – Shaping Your Imaging solutiONS
A miniaturized digital microscope subsystem designed for giving your life science instrument the power to see.
Multifluorescence
Optical microscopes have propelled research findings in life sciences and diagnostics for several centuries - microscopy and digital imaging is central to life sciences research, as well as clinical diagnosis and drug discovery. Making the unknown visible is the overall challenge in this disciplines and the key for success.
Digitalization, miniaturization, automation – integrated digital microscopic imaging enables tailored process automation, designed to suit the application to the fullest.
Now, JENOPTIK SYIONS® supports you to be more innovative for a better future.
The electronic & software modularity approach gives you the freedom to develop minimum viable products in a record time and thus rapid prototype testing becomes more easy.
If you are interested in developing innovative life science applications, then JENOPTIK SYIONS® is your partner of choice for rapidly constructed, miniaturized optical engines that will fit into any instrument.
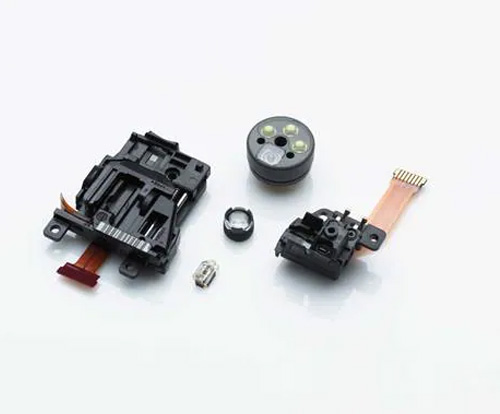
Microscope camera
- Microscopy Imaging from Jenoptik Brings the Full Power of Your Microscope to Light
Jenoptik’s sensitive, high-resolution USB cameras upgrade every microscope to a cutting-edge digital microscope workstation.
The JENOPTIK GRYPHAX® series is specifically designed for microscopy imaging and easy to use with any microscope — whatever the brand, thanks to the C-mount interface. JENOPTIK GRYPHAX® cameras provide brilliant, low-noise images with reproducible and true color. Short exposure times and high image refresh rates make the system time-efficient and convenient to use. This means you can position and focus your camera quickly and easily, even on moving objects. The USB cameras can even deliver live images at video speed in brilliant quality thanks to the state-of-the-art CMOS-sensor technology used in the camera series. The user-friendly and intuitive microscopy imaging software is part of every camera package contents (including future updates), runs on WIN / MAC / LINUX. In addition, there are many other 3rd-party software options for microscopy imaging as well as a free SDK.
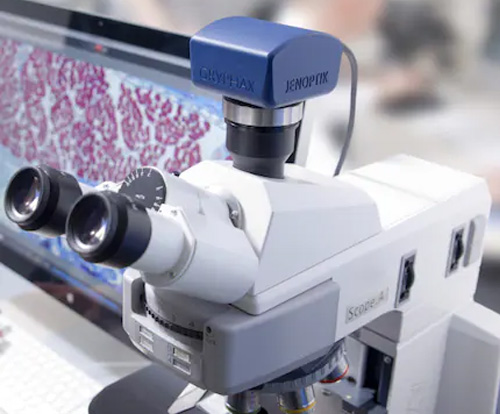
Polymer-based camera modules
- Maximum resolution on smallest surfaces thanks to polymer camera modules from Jenoptik
Our highly efficient, polymer-based camera modules feature a space-saving design, making them ideal for use as image sensors in digital cameras, for example. This saves weight as well as costs.
Jenoptik develops and produces polymer-based camera modules with digital image sensors, which offer maximum resolution on the smallest surfaces. The precision optics are perfect for use in digital cameras. Polymer optics are also ideal for use in the automotive sector as well as in industry and medical technology.
The production process for optical systems with lightweight plastic modules is considerably less elaborate than for other optics. This allows you to reduce both weight and costs, while maintaining the same level of performance.
Benefits:
- Powerful: maximum resolution on the smallest surfaces
- Customer-specific: highly complex camera modules for your specific applications
- Cost-efficient: significantly fewer elements required for polymer-based optics
- Leading manufacturer: benefit from expert knowledge and sophisticated injection molding technology
- Complete technology chain: Jenoptik offers design, development, manufacture and assembly
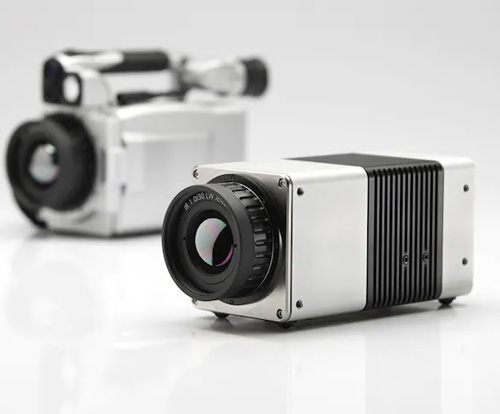
Thermographic Cameras
- Thermographic cameras and infrared camera modules for stationary and mobile use
The handheld and stationary thermographic camera impress with their high level of measuring accuracy and pin-sharp thermal images.
The thermographic camera and the infrared camera modules measure two-dimensional temperature distributions in a fast and non-contact process. Thanks to the high resolution of our infrared camera systems, even the smallest differences in temperature are visualized in minute detail. As such, the thermographic camera is characterized by its exceptionally high and reliable level of measuring accuracy.
The thermal imagers are the product of over 25 years of expertise in the field of camera technology and infrared optics. With an image resolution of up to 3.1 IR megapixels, the devices set new standards and make Jenoptik the technological market leader and a pioneer in ultra-high-resolution uncooled thermographic cameras.
Benefits Thermographic Camera
- Extremely precise: World's highest spatial resolution of up to 3.1 IR megapixels for a high level of measuring accuracy.
- Efficient: Capture wide measuring ranges in high resolution.
- Fast: Radiometric imaging in real time.
- Robust and durable: Saves you time and costs, as uncooled cameras require no maintenance.
- Technologically sophisticated: More than 25 years of experience in developing and producing infrared cameras.
- Flexible: Wide range of connection options enable the thermography cameras to be installed in customer-specific systems.
Laser and Laser Technology

Comprehensive laser-based solutions for applications in health care and industry
From laser components to automated laser systems
Jenoptik develops and manufactures comprehensive laser technologies across the entire value chain at various levels of integration for a multitude of application environments. We are your OEM solution provider with a broad product portfolio consisting of state-of-the-art laser products, starting from the core: the epitaxial wafer structure. Depending on your specific needs, our products are available as individual components, modules, complex systems or even robot-based machines.
Thanks to our long-standing expertise in the field, we provide customized laser solutions that can be easily integrated into existing systems or purchased as automated systems. Coupled with our energy-efficient technologies, this means maximized precision and productivity yet minimized waste and risk.
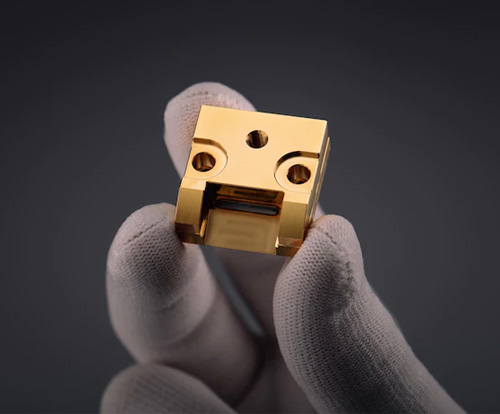
OEM Laser Solutions
- OEM laser solutions based on diode- and disk laser technology
Laser-based solutions for medical applications, materials processing, optical pumping, illumination and sensing
Within the product segment OEM laser solutions, we focus on developing, manufacturing and selling custom design:
- high-power diode lasers
- diode-pumped disk lasers
- laser sub-systems
Our OEM laser solutions serve applications in healthcare such as laser-based therapy and diagnostics, materials processing and optical pumping.
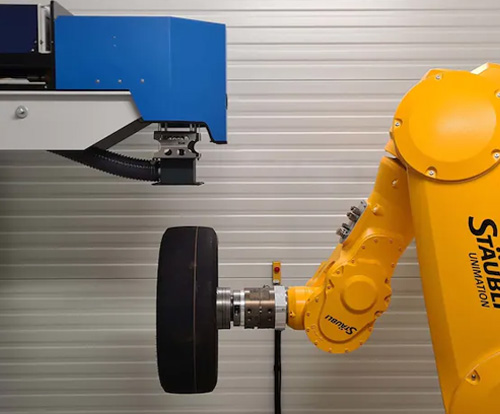
Laser Ablation
- Material ablation with the power of laser for innovative machining processes
The new Jenoptik JENscan® product family makes new production processes possible. Material ablation with a high-performance laser for the highest precision and process stability.
Laser ablation makes it possible for structures to be machined that were beyond the capabilities of conventional machining, and it replaces the tools that have previously been used in mechanical machining, which wear out. Dust, dirt and numerous manual work steps are gone, replaced by shorter development and prototyping times and series production with perfect machining results every time.
Benefits of laser paint ablation
- Possible to create any design or pattern
- Very large patterns can be removed seamlessly
- Large 3D shapes can be machined
- Highest precision
- Most filigree structures and lines
- Component deviations are compensated automatically
- Fully automated process without manual pre-machining or finishing
- No tool wear
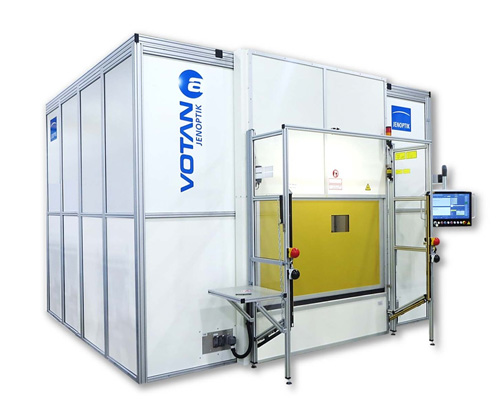
Laser Scoring
- Precise laser – airbag weakening for reliable airbag tear lines.
Jenoptik’s advanced laser technology enables airbag weakening in all components of the vehicle interior and supports the passive safety systems of modern vehicles.
For optimum performance of passive safety systems – such as passenger airbags – it is essential to introduce precise tear lines in components of the vehicle interior. With Jenoptik technology, the airbag is weakened with a laser, which very gently removes material, with minimal heat input, without putting mechanical stress on the components. The laser is a tool that, unlike all mechanical processes, never becomes blunt, so that all component parts can be manufactured under exactly the same conditions. In addition, the non-contact machining process does not produce any chips. The resulting smoke is extracted without leaving any residue and cleaned off in an environmentally friendly manner.
The tear lines themselves can be created by making a large number of pocket holes with or without residual wall thickness or with slots in any possible combination and with any kind of geometry, as per customer requirements. The airbag opening force can be adjusted by changing the parameters of the tear line – for the best possible airbag performance.
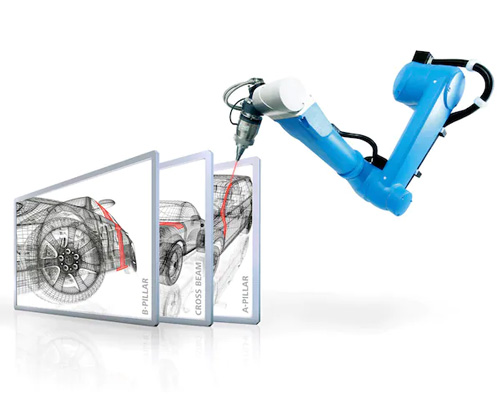
Laser Cutting
- Precise laser cutting of 3D plastic and metal components
The non-contact laser cutting system from Jenoptik provides a quick way to process metals and plastics. The non-wear process from Jenoptik guarantees low maintenance costs.
Jenoptik is one of the world’s leading manufacturers of laser machines and laser systems for material processing. We develop and build efficient laser machines for your specific production requirements, helping you to realize new manufacturing opportunities. Your process requirements, production environments and specific goals are our benchmark. We configure and optimize our modular standard platforms in close cooperation with you to deliver a tailored solution — because progress needs a base of excellence.
Jenoptik experts will help you to find the best processes for your laser application in production, allowing you to process different materials such as metals, plastics, semiconductors, textiles and leather efficiently and cost-effectively. We offer highly developed laser beam sources such as diode, solid-state and fiber lasers, as well as laser machines tailored to the relevant process. These are ideal for a range of different industries — from the automotive industry to sciences.
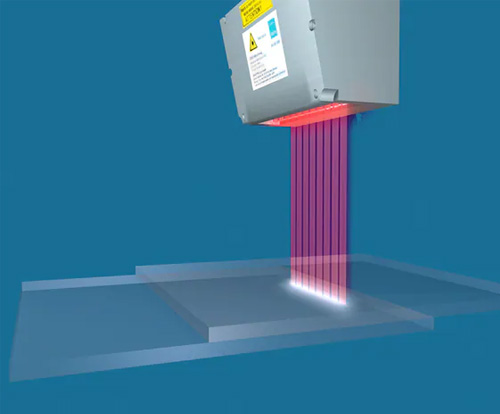
Laser Welding
- Precise and extremely strong welding of plastics with energy-efficient laser welding
Laser welding allows you to join plastic parts with an extremely strong bond. The process is non-contact and vibration-free, which helps protect the material.
With laser welding, you can join plastic parts quickly and precisely while saving energy, creating strong and durable weld seams that do not leave a visible mark. This means that plastic welding using laser technology also meets the highest aesthetic demands.
The process is completely non-contact and vibration-free, and the energy input is precisely metered, which means the joined components are subjected to minimal thermal and mechanical loads. At the same time, laser welding is a particularly clean process. Processing does not create any emissions, has no flash and does not cause any burr formation.
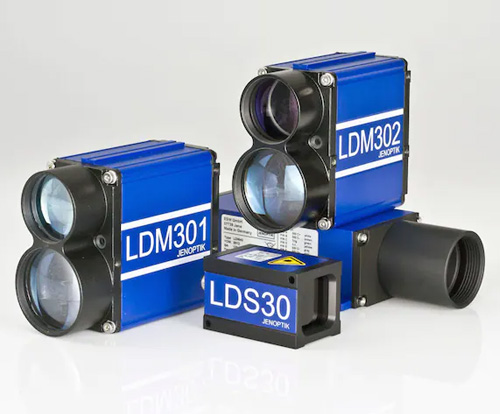
Laser Distance Sensors
- Laser Distance Sensors for long measuring ranges and millimeter accuracy
Proven technology for measuring distances and positions – ready to integrate in industrial applications.
Jenoptik laser distance sensors monitor or measure distances or object lengths, provide positional location, and determine fill levels from a few centimeters up to three kilometers in a non-contact fashion. These distances are measured with an accuracy of up to one millimeter and at a output rate of several thousand readings per second. The measured object can be a solid, energy absorbing or radiating hot body. Especially measurements on natural surfaces with low reflectivity are also possible. The laser distance sensors even can measure distances to or from moving objects.
The industry-proof housing with compact footprint and industry standard interface options make the laser distances sensors ideal for integration into your automation and process control systems. The distance sensors are available with RS-232, RS-422, Profibus, or SSI interfaces and bus systems. Along with digital switching and analog output the sensors easily adapt into automation environments. The ruggedized housing with integrated heating enables installation where needed – even in harsh industrial environments.
LiDAR Technologies
-
Innovative LiDAR Technologies: Optical Modules and Components for LiDAR Sensors
Delivering the Power of Light – For more efficiency, safety, and autonomy.
LiDAR sensors are a key technology of the future for process automation or highly automated, fully automated and autonomous driving. In conjunction with cameras and radar sensors, they perceive the surroundings, help with orientation, detect obstacles, measure distances - and thus ensure greater safety and efficiency on busy roads and in automated industrial environments. 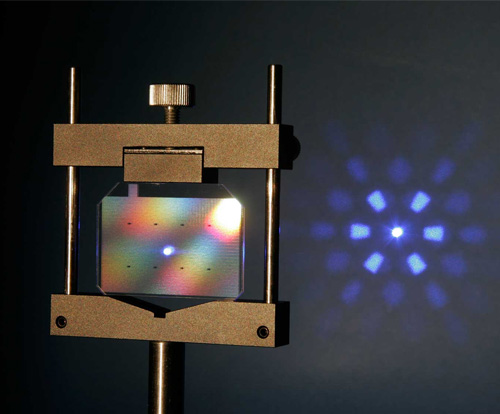
Diffractive Optical Elements - DOEs
- Diffractive Optical Elements for High-precision, Energy-efficient Laser Applications
Jenoptik provides you with diffractive optical elements tailored to your specific laser applications and system requirements. This allows you to efficiently shape your light and improve overall system performance and flexibility.
Diffractive optical elements (DOEs) shape and split laser beams in an energy-efficient manner. You can implement a wide range of applications with minimal light loss – examples of diffractive microoptics can be found in production facilities for laser material processing, in medical laser treatments and diagnostic instruments, in areas such as lighting, printing technologies and lithography as well as in measuring and metrology systems. DOEs are used to pattern light in work areas for custom illumination. Jenoptik offers DOEs for all wavelengths across the spectrum, however, we have unique experience with 193 nm and EUV.
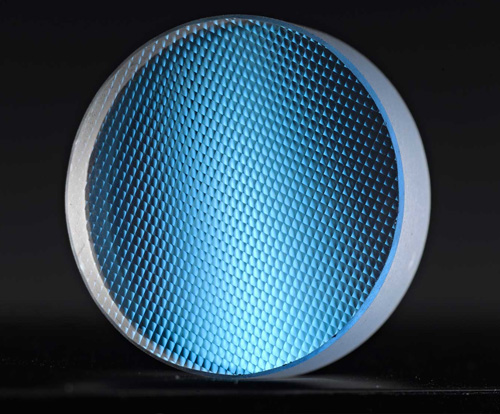
Refractive Optical Elements - ROEs
- High-precision Refractive Optical Elements (ROEs) for Diverse Applications with High Efficiency
Jenoptik produces refractive optical elements (ROEs) tailored to your individual application. We do this by working closely with you during the development process.
Jenoptik designs and manufactures high-precision refractive optical elements (ROEs), such as micro lens arrays and homogenizers, which can be used for diverse applications. We work to your specific requirements and, thanks to short production times and close cooperation, we can contribute to your success as early as the development phase.
With our sophisticated microoptics, we can implement a multitude of functions with minimal light loss.
These include:
- Fiber and waveguide coupling for information and communications technologies
- Homogenization of light over a specific area
- Laser beam shaping for converting existing beam profiles into customer-specific intensity profiles
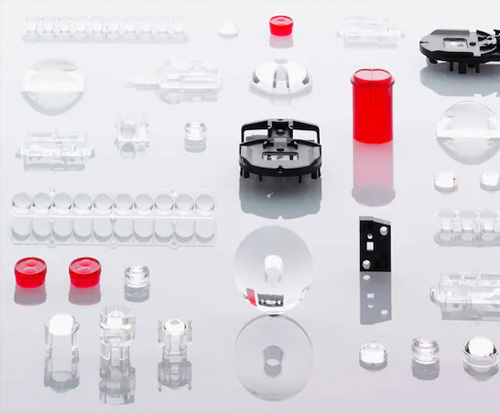
Polymer Optics
- Complex Polymer Optics: Components and Systems Using Sophisticated Injection Molding Process from Jenoptik
For more than 50 years, we have been developing and manufacturing polymer optical components and complex optomechanical electronic systems for our customers using sophisticated injection molding process.
Jenoptik designs, develops, manufactures and assembles highly complex polymer optical systems and components: We offer extremely high performance and precise polymer micro optics. With a variety of dimensions, geometries and coatings available, they match your specific applications perfectly.
We use lightweight polymers and cover the complete technology chain - from the design of parts, modern 2K injection molding processes and highly technical tool construction through to specialized coating technology.
We are constantly developing our technologies and processes further, so our production methods and capacities ensure you benefit from the most efficient production processes - from prototypes through to large-scale series production.
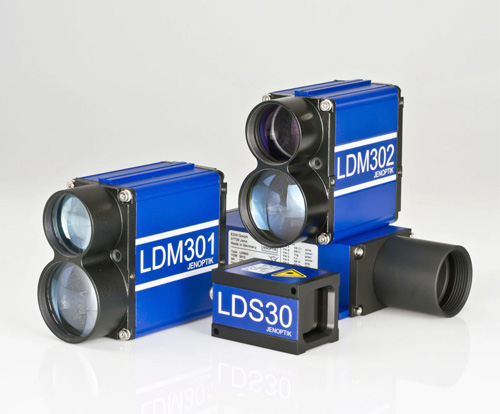
Laser Distance Sensors
- Laser Distance Sensors for long measuring ranges and millimeter accuracy
Proven technJenoptik laser distance sensors monitor or measure distances or object lengths, provide positional location, and determine fill levels from a few centimeters up to three kilometers in a non-contact fashion. These distances are measured with an accuracy of up to one millimeter and at a output rate of several thousand readings per second. The measured object can be a solid, energy absorbing or radiating hot body. Especially measurements on natural surfaces with low reflectivity are also possible. The laser distance sensors even can measure distances to or from moving objects.
The industry-proof housing with compact footprint and industry standard interface options make the laser distances sensors ideal for integration into your automation and process control systems. The distance sensors are available with RS-232, RS-422, Profibus, or SSI interfaces and bus systems. Along with digital switching and analog output the sensors easily adapt into automation environments. The ruggedized housing with integrated heating enables installation where needed – even in harsh industrial environments.ology for measuring distances and positions – ready to integrate in industrial applications.
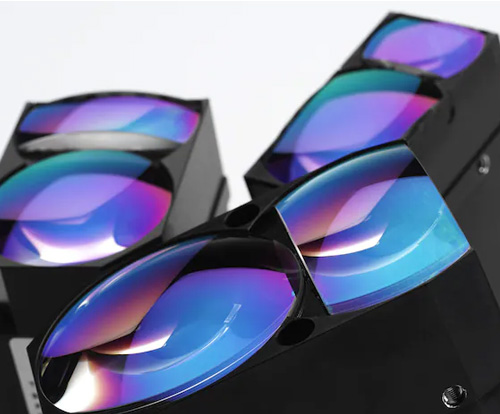
Laser rangefinders for mobile and stationary systems
- Laser rangefinders for mobile and stationary systems
Our laser rangefinders quickly and precisely measure the distance to non-cooperative targets, even under the most difficult measurement and visibility conditions.
Laser rangefinders from Jenoptik deliver fast and precise distance data while at the same time offering a long measuring range – even in difficult measurement conditions. Even with poor visibility and in extreme temperatures, the devices quickly and reliably measure the distances to non-cooperative targets. This enables you to assess situations immediately and respond to threats quickly and in the appropriate manner.
The extremely compact and lightweight modules from the DLEM series are ideal for integrating into handheld and weapon-mounted systems. These devices quickly and precisely measure targets at a distance of up to 5 kilometers.
The solid-state laser rangefinders from the ELEM series are also compact and offer an extremely long measuring range of up to 40 kilometers. These rangefinders are perfect for both mobile and stationary applications, e. g. fire control systems.
Optics and Optical Systems
Your system partner in optical solutions and technologies
Jenoptik enables innovation with its product lifecycle management and industry-leading optical technologies and solutions, from component to system level. Our expertise enhances value in the the semiconductor and electronics, mobility, healthcare and life sciences and material processing industries.
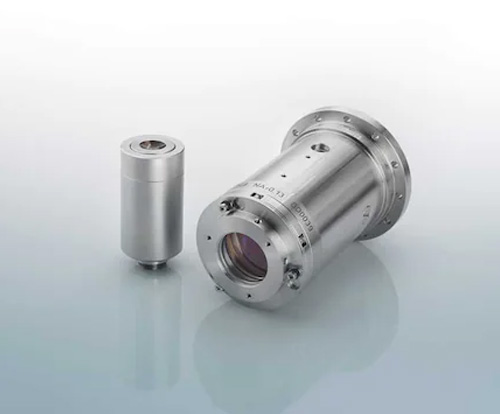
Customized and Standardized Objective Lenses
- The Perfect Optics Solution
Jenoptik offers customized and standardized objective lenses or optics, adapted precisely to your diverse and highly complex applications — helping you to secure sustainable success.
You can benefit from our extensive expertise and range of services. We can provide you with the complete chain of technology from one source — from development to design and production through to system integration. Right from the outset, Jenoptik finds the perfect balance between standard products and special developments, contributing to your long-term success — and saving your time and money.
Taking this approach, our specialists and engineers have very successfully developed many customized objective lenses, which are manufactured in large quantities today.Go forward into the future with us: We will analyze your technical requirements, work with you and create an optics solution optimally tailored to your needs!
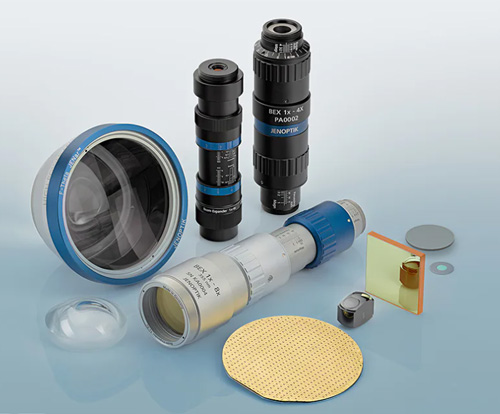
Objective Lenses for Laser Material Processing
- F-Theta objective lenses, beam expanders and OEM sub-systems for high precision in laser material processing
Jenoptik offers high-precision laser beam expanders, F-Theta lenses and smart, ready-to-install plug-and-play solutions for use in demanding series production or scientific applications.
Whether it is cutting, welding or engraving, photonics play an integral role in countless application areas of laser material processing. Thanks to our state-of-the-art laser technologies and optical solutions, a wide variety of materials can be processed with high productivity and precision. We are your reliable partner for machine-integrable optical components and systems that are designed for your precise requirements in material processing.
Our reliable and durable products are of the highest precision and quality. We constantly expand our product portfolio through our proximity to the customer, market and applications, which is also evident in the F-Theta lens series JENarTM, JENarTM APTAlineTM and JENarTM SilverlineTM. The suitable Fix-BEX beam expander, variable BEX or motorized BEX-M can also be combined for specified applications accordingly.
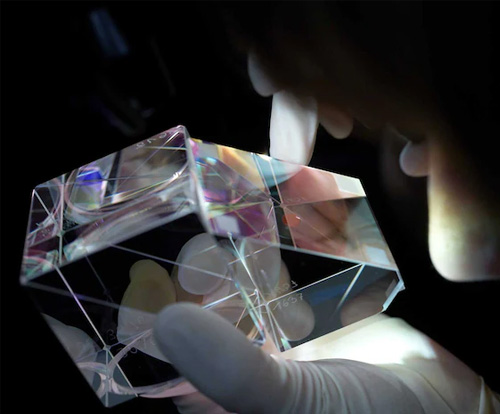
Precision Optical Components
- Microoptical and Optical Precision Components: Use Light for Measurement, Analysis, Structuring and Processing with a High Level of Reliability
Jenoptik offers precision optical components made from a variety of optical materials, in various shapes and with numerous coatings, to cover the entire optical spectral range — tailored to suit your applications.Customer-specific products, from the prototype through to series production: We count high-precision optical elements and optical thin film elements as some of our core areas of technological expertise.
Jenoptik is one of few providers worldwide to manufacture precision optics in virtually any optical material. These materials include optical glasses, glass ceramics and crystals, as well as modern and lightweight polymers.
Optical Test and Measurement Solutions
Our application-specific test, measurement and manufacturing solutions are based on innovative technology, sophisticated software, high quality and customer intimacy.
We offer standard but also customized solutions according to our customer’s needs from idea to mass production.
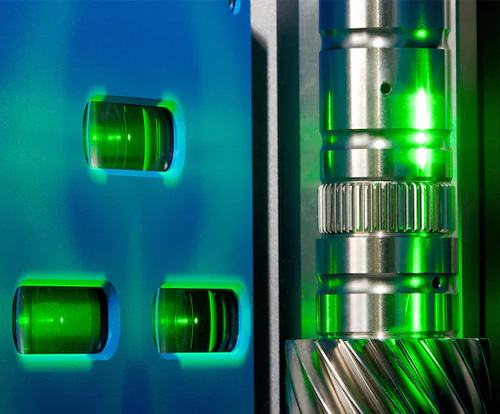
Optical Shaft Measuring Systems
- Optical Shaft Measuring Technology: Measuring Systems from the Opticline Range
Jenoptik has developed a new generation of optical measuring systems that make quality control during production easier.
For many years, the Opticline range of measuring systems have set the benchmark in optical shaft measuring technology. They boast an impressively high measurement speed, precision, and optimum ease of use.
In 2015, a new generation was launched, offering several technical innovations and optimizations. Our systems allow efficient and transparent quality control in production.
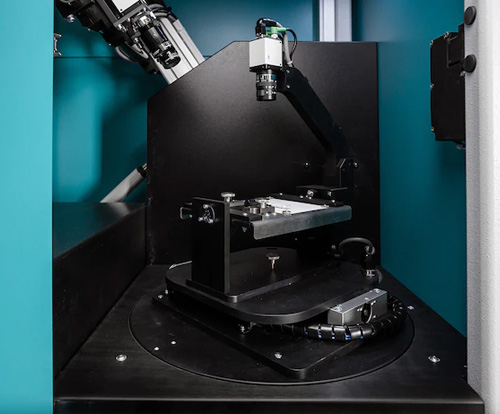
Optical 3D Measurement Technology
- Optical 3D measurement technology for high point density and accuracy in all phases of production
We offer optical 3D scanners based structured-light projection technology for highly accurate and automated part inspection. The FLEX-3A product line is designed for the incoming goods department, toolmaking, initial sampling and release, as well as for automated inspection during production.
The high-resolution scan data is capable of being compared directly against a CAD model, or used for dimensional, shape, and positional tolerance measurements. With object point resolutions down to 5 um, as well as our smart multi-image referencing using virtual targets, the FLEX-3A is ideally suited for high-precision automated 3D inspection of complex small parts.
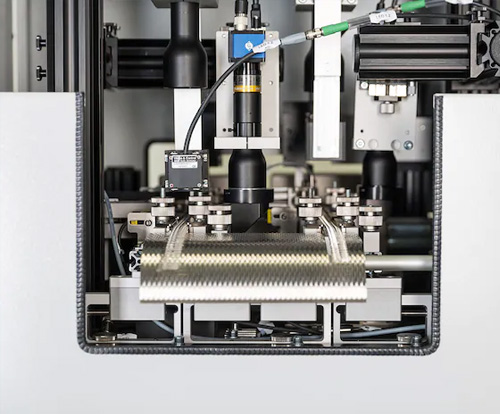
Optical In-Line Inspection
- Test stations for the optical inspection of stamped parts
The demands for efficiency and cost structure in stamped part production have grown rapidly. Manufacturers of stamped parts need competitive solutions that enable zero-defect production despite increasing process complexity.
PSS inspection stations are an innovative leap from the traditional random inspection of stamped parts, to the fully automated in-line, inspection, measurement and sorting of stamped production parts.
Real-time delivery and processing of each manufactured part’s inspection data, from the first punching stroke onwards, allows shorter and more efficient changeover processes, high stamping line utilization, and the lowest possible consumption of resources. For our customers, this means improved quality at lower costs.
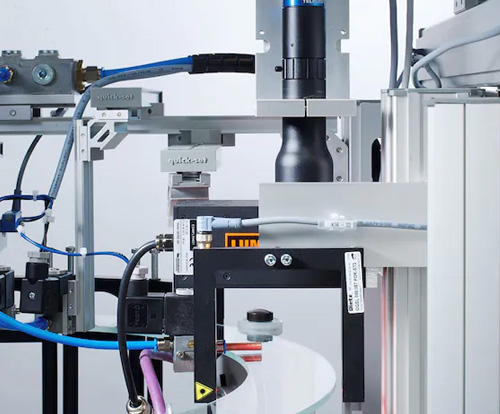
Vision-Systems
- Our powerful Vision-Systems realize complex optical inspection tasks.
Our multi-sensor capable vision systems have the capability of operating multiple cameras in parallel, or serially, and having very short cycle times allowing high part throughputs to be achieved. The multilingual software is very easy to use, with a comprehensive function library for 2D as well as 3D applications and enables detailed data management (e.g. statistical analyses).
Jenoptik vision systems can be integrated into machines, systems and tools, used in laboratory setups, or form the heart of complete inspection and sorting systems. They are fully capable of communication via multiple types of interfaces. They are indispensable in process automation and enable tool and process monitoring as well as processand quality control.
Typical inspection tasks
- High-precision external contour inspection of components
- Position detection
- Presence, completeness, and position control
- Attributive tests
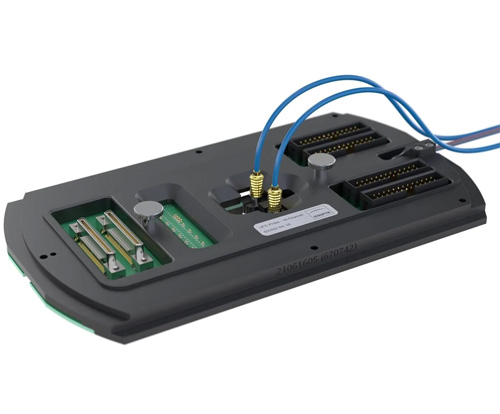
Ultra-fast opto-electronic probe card
- UFO Probe® card – new test card for PIC wafer testing
Photonic Integrated Circuits (PICs) are the chips of the future. Integrated photonics use light instead of electricity for data and signal processing.
The UFO Probe®card is the tool for simultaneously testing the optical and electronic functionalities of PIC. The Jenoptik probe card is based on a concept for optical scanning of photonic integrated circuits, which is insensitive to alignment tolerances of the wafer sampler. The opto-electronic test card can, therefore, be used with commercially available wafer samplers and ensures a correspondingly high throughput when testing photonic integrated circuits.
Optoelectronics and Optoelectronic Systems
Optoelectronics: Products and Customer-Specific Systems Using the Latest Technology
Jenoptik supports you in the production of optoelectronic systems and components that are perfectly tailored to your requirements.
We offer a broad range of development services and products covering optical system solutions and components in the area of optoelectronics. We also develop from prototype and manufacture to series customer-specific systems that are perfectly tailored to your individual applications and requirements. We support you from the initial idea and the design stage through to production, assembly and quality control, including supply chain management.
The many years of experience and comprehensive expertise of our experts enable us to combine optics, electronics, mechanics and software in our solutions. This gives you a competitive edge, allowing you to concentrate on your core competencies. You also reduce cost and resources. You can outsource the risk of production, while benefitting from faster market launch times.
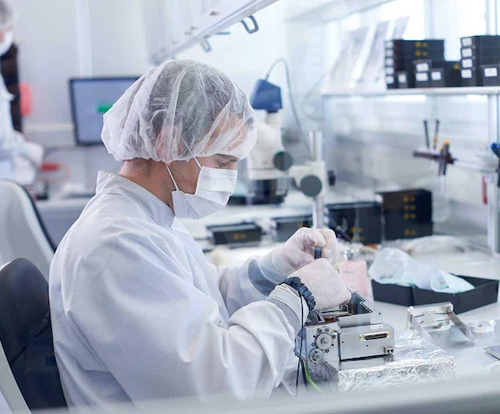
System Partner for Optoelectronic Systems
- System Partner for Optoelectronic Systems: Achieve Your Objectives Quickly and Reliably
Our highly developed, customer-specific components and modules contribute significantly to the commercial success of our OEM customers.
Jenoptik is one of the leading developer and manufacturers of optoelectronic high-performance components. Our success is based on many years of experience and in-depth knowledge in optic-electronic and mechanical technologies. Our company incorporates a wide range of this technologies as system application. We use this extensive expertise to develop optoelectronic systems that are precisely tailored to your requirements. At the same time, you benefit from faster market launch times. This makes us the ideal system partner for OEM customers.
We integrate optics, electronics, mechanics and software in accordance with your customer-specific requirements and develop future-oriented optoelectronic systems. We are on hand as your expert contact partner throughout your project and beyond. We cover the entire value chain and cost down principles: Our experts plan and develop systems and procedures, manufacture components, assemble these components in the overall system and take care of supply chain management.
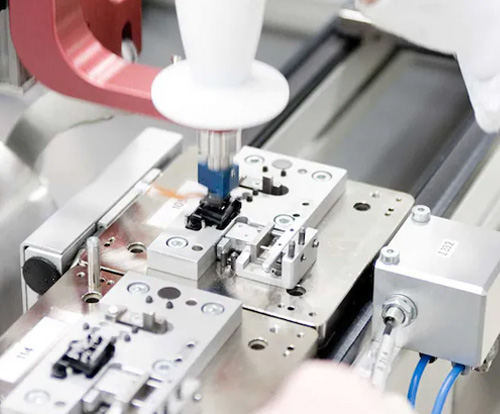
Customized-Specific Optoelectronic Systems
- Optoelectronic Systems for Your Individual Requirements
Jenoptik develops optoelectronic systems and modules that you can integrate into your existing systems in line with the specific application, saving you both time and money.
We manufacture optoelectronic systems that precisely meet your requirements. We develop integrated solutions for your market that intelligently combine optics, lighting, electronics, sensors and software.
Jenoptik is your reliable partner along the entire value chain: We support you from the initial idea through to the design stage, development and series production, including supply chain management. You will benefit from our many years of experience and the broad expertise of our highly qualified employees. Outsource the development and production of your optoelectronic systems without any risk, while saving costs and avoiding the use of unnecessary resources.
Jenoptik offers customer-specific optoelectronic systems in the following areas:
- System solutions for polymer optics
- Ultra-precision technology
- Electronics development
- Software and firmware development
- Digital image processing systems
- Solutions for connection technology, AVT
- Solutions for packaging sensor chips
- Development, prototype construction, series production
- Lighting technology and LED development
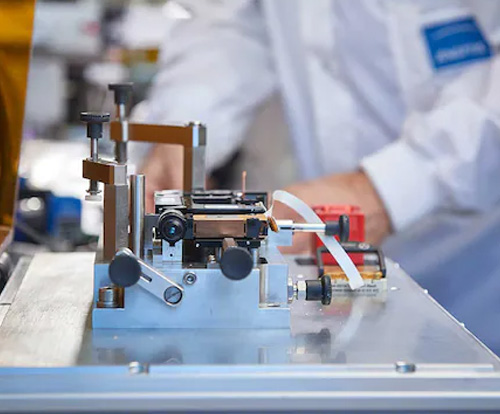
Optoelectronics Assemblies and Subsystems
- Highly effective assemblies and subsystems in the field of optoelectronics
As a reliable development and production partner, Jenoptik provides you with optoelectronic assemblies and subsystems, while also assisting with system integration.
We offer combined competencies to ensure your success: From the optics division, for example, we supply high-quality glass and polymer optics, free-form optics and mirrors. Our semiconductor division provides active components such as color sensors and light-emitting diode. We take charge of the circuit design and develop suitable software. We then assemble the optical components with maximum precision in clean-room conditions.
We can thus provide you with optoelectronic assemblies and subsystems that are tailored to your specific application. We also coordinate our production and logistics concepts with your supply chain.
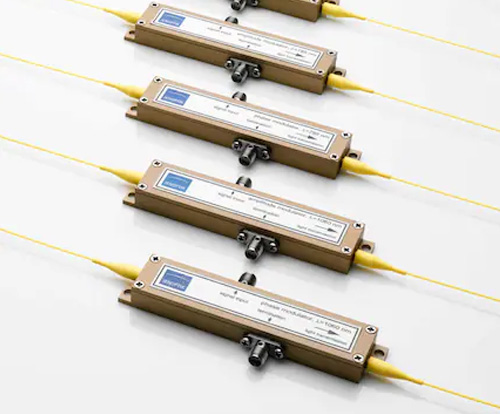
Light Modulation
- Light Modulation from Jenoptik: Custom-Made Modulators for a Wide Range of Applications
In order to modulate light according to your requirements, Jenoptik offers you various integrated optical modulators and liquid crystal based modulators, as well as the appropriate control unit.
Jenoptik light modulators are ideal for the amplitude, phase and polarization modulation of laser light in the visible and infrared spectral range. Our products are perfectly tailored to your applications: In addition to standard light modulators, Jenoptik also develops and manufactures customer-specific components.
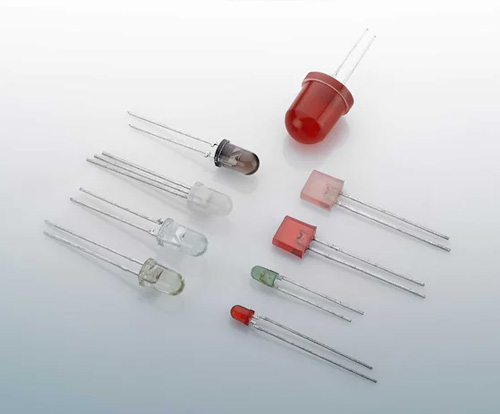
Photodiodes and LEDs
- Photodiodes and LEDs: spectrally selective, powerful and durable
The photodiodes and LEDs from Jenoptik can be easily integrated into your existing systems or adapted to optoelectronic applications, and can also eliminate the need for external filters.
We offer a wide range of photodiodes and LEDs in different housings, which you can easily integrate into your existing systems. We can develop and manufacture tailored, customer-specific modules for sensor-based applications with optimized chip-on-board technology, in which uncapped chips are mounted directly on the PCB, thus ensuring optimum heat dissipation combined with minimal space requirements.
Jenoptik photodiodes can be used to detect light, IR or UV radiation. Our photodiodes are characterized by their high long-term stability, optical filters integrated at chip level and excellent signal-to-noise ratio.
Road safety
Increase road safety – with a reliable partner at your side
Jenoptik's specialists help you to effectively increase road safety from planning and implementation through to maintenance and repair.
Jenoptik as a reliable partner at your side supports you to increase road safety by reducing speeding and red light violations and automatically recording number plates. We have individual products and services as well as complete traffic solutions to meet whatever requirements you have.
Jenoptik specialists provide competent advice on every aspect of road safety and work with you on how best to implement traffic enforcement systems. We analyse local situations, develop concepts and financing models, install the appropriate systems, train your staff, prepare the results and maintain your systems. You can then increase safety at hazardous road sections and reduce accidents at multi-lane junctions or motorways, in tunnels, on country roads and at public buildings in urban areas.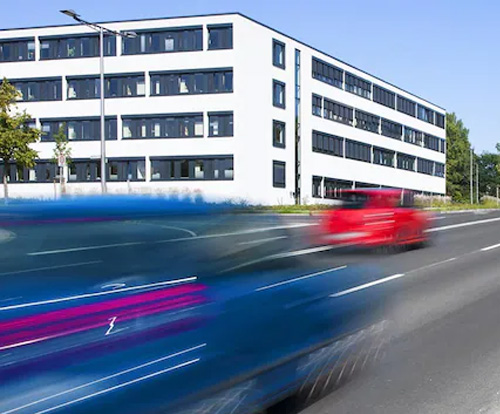
Speed enforcement
- Speed enforcement increases road safety
Jenoptik's mobile, semi-stationary and stationary speed enforcement systems helps reduce road accidents.
Speed enforcement increases road safety. Jenoptik's highly advanced systems help to significantly reduce accident numbers. Our equipment can be used at accident blackspots, busy junctions, in traffic-calmed areas such as kindergartens and old people's homes, and on hazardous road sections such as on motorways, tunnels and country roads. Specific locations or longer road sections can be monitored.
State-of-the-art laser and radar sensors deliver measurements you can depend on. They not only detect speeding vehicles, but also vehicles in wrong lanes, overtaking offences and illegal turns, and are able to simultaneously monitor multiple lanes in both directions. High-resolution cameras automatically document traffic violations with vehicles being clearly identifiable in the images, even in the dark or in bad weather conditions. The images are legally admissible and will stand up in a court.
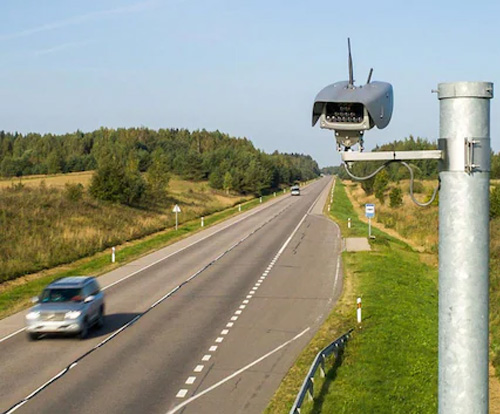
Average speed cameras
- Average speed cameras improving road safety
Jenoptik average speed cameras increase safety along hazardous road sections. They provide improved and safer traffic flows and therefore lower emissions.
Average speed cameras are regarded as one of the surest ways of increasing safety along hazardous road sections, e.g. at tunnels, bridges, motorways and roadworks. Jenoptik's systems have also been proven to help improve traffic flow and reduce CO² emissions. Speed measurement begins when a vehicle enters a specified road section. A high-resolution average speed camera records the number plate using state-of-the-art cryptological technology, together with a time stamp. When the vehicle exits the road section, the number plate is re-captured by the average speed camera. The two anonymous data records are compared and an average speed calculated as evidence of speeding.
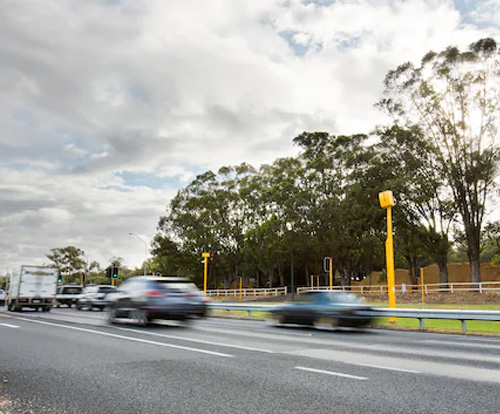
Red light cameras
- Innovative red light camera systems for combined speed and red light enforcement
Jenoptik offers red light camera systems which can also be simultaneously used for speed enforcement, thereby increasing traffic safety.
Red light violations, illegal turning, driving in the wrong lanes and speeding are the main causes of fatal road traffic accidents, especially at junctions. By using Jenoptik's innovative and individually adapted red light camera systems, traffic can be monitored and infringements prosecuted while saving on resources. A single device can be used for all requirements. Traffic safety is then increased and accidents reduced.
The red light camera systems are based on state-of-the-art radar technology and induction loops combined with high-resolution cameras. These provide legally admissible images. The systems enables multiple lanes to be monitored simultaneously. Different speed limits can also be set for different vehicle types, e.g. cars and trucks. We offer devices that can be used flexibly for various purposes and at different types of location. Because every junction is different, we customise our products and services to meet individual needs.
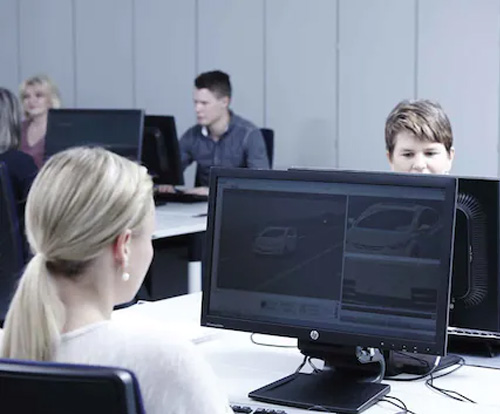
Evaluation software
- Professional evaluation software for traffic safety
Jenoptik's evaluation software efficiently and reliably processes large data volumes including data pre-processing for downstream procedures.
The TraffiDesk™ pro evaluation software efficiently and securely processes data from traffic enforcement systems. It delivers reliable performance even for large data volumes, easily processing in excess of 80,000 traffic violations per day. The back office software also pre-processes data for downstream procedures and can be scaled as required: from single- and multi-user systems through to large-scale processing centres. Processes are fully documented for legally admissible evidence in courts.
TraffiDesk™ pro imports and verifies data, checks quality and prepares and exports cases for downstream procedures. It's modular design enables it to be optimally adapted to your specific workflows. Automated processing reduces time, minimises errors and fully documents individual work steps. Evaluation is then faster and output is high quality. Your measuring locations, systems and users can be managed via the back office software.
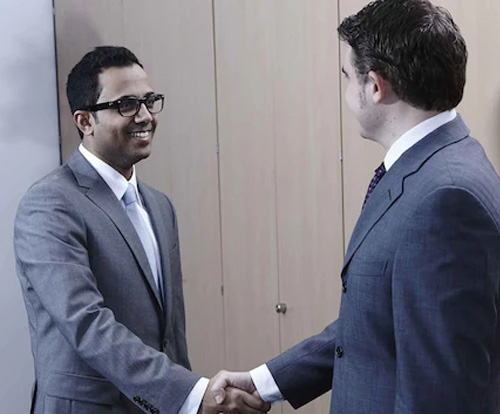
Traffic Service Provision
- Financing models and services from specialists for traffic enforcement
Jenoptik supports you in traffic enforcement by increasing road traffic safety, reducing risks at hazardous road sections and reducing the number of accidents.
Many city and municipal authorities around the world face the challenge of increasing traffic safety. The task is not easy especially with low budgets and personnel numbers available for efficient and modern technologies. Jenoptik's specialists therefore offer comprehensive services and a range of financing options that do not use public budgets or involve financial risks.
With many years of experience, we are a strong partner whether you want to lease equipment or require support with processing data or equipment maintenance. Jenoptik's products for stationary, semi-stationary and mobile traffic enforcement can be deployed flexibly for various purposes and supplemented by our range of services. DEKRA annually inspects our work procedures and data transfers so we can guarantee EU GDPR compliance on data privacy. Jenoptik also provides single-source services ranging from product development and system installation through to customer service, support and financing.
Civil security
Civil security: Safeguarding communities and borders through advanced ANPR solutions and next generation technologies.
Working with Jenoptik to combat organized crime and terrorism: Our systems for civil security help you to prevent and solve crimes.
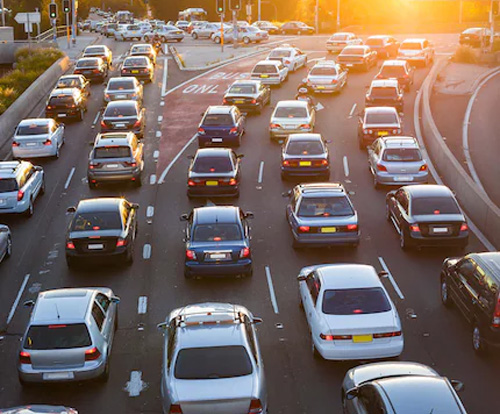
Automatic number plate recognition (ANPR)
- ANPR: Highly advanced technology for automatic number plate recognition
Automatic number plate recognition (ANPR) is particularly powerful, classifying vehicle type and recording number plates worldwide.
Police and security authorities worldwide are using automatic number plate recognition (ANPR) for various purposes such as border and toll controls, and to increase civil security. Jenoptik's highly advanced technology has been proving itself in international projects for more than 30 years. Our experts are constantly presented with new requirements and are developing individualised products to precisely meet customer needs.
Jenoptik´s deep learning software makes ANPR particularly powerful by being able to extract even more information from recorded images. The software reliably differentiates between vehicle classes such as passenger cars, vans, lorries, buses and motorcycles. It can also recognise practically any of the world’s number plate types. The software integrates into the ANPR cameras so no additional equipment or installation is required, and achieves far better results than conventional visual technologies.
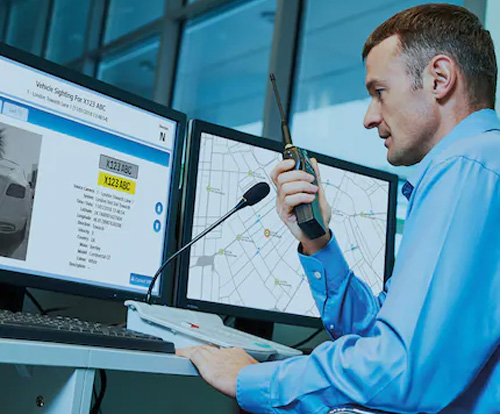
ANPR data analysis software
- Data analysis software: Targeted processing and evaluation of number plate data
TraffiData analysis software evaluates number plate data in real time and is generating easy to read reports to increase civil security worldwide.
ANPR data analysis is helping police and security authorities around the world to increase civil security. ANPR cameras continuously record vehicle number plates while TraffiData analysis software filters and clearly displays the required information. From the huge amount of ANPR data, personnel on the ground can then automatically obtain the information they need, saving on costs and resources.
TraffiData analysis software also uses sophisticated algorithms to identify patterns, e.g. two or more vehicles frequently seen driving together, quickly identifying potential threats. TraffiData can help to provide an indication of where a vehicle may travel next, based on previous patterns and behaviours. Filters can also be set to alert authorities when a vehicle is detected within a specific area, helping to protect high-risk locations such as connecting roads, city centres, airports, critical infrastructures and public buildings.
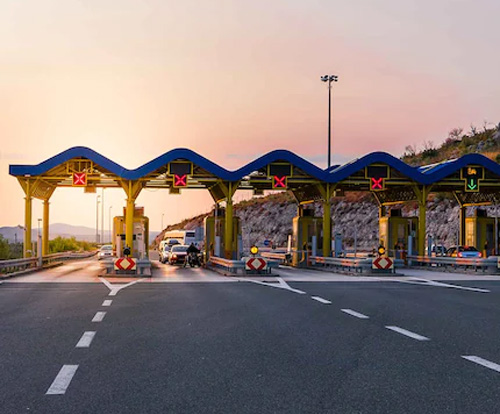
Border security
- Border security: Record and analyse ANPR data in real time
Increased civil security: VECTOR² cameras and TraffiData analysis software record vehicles at borders and evaluate ANPR data in compliance with legal requirements.
Law enforcement agencies use automatic number plate recognition (ANPR) to monitor and control all borders. With the VECTOR² camera and TraffiData solutions, Jenoptik can assist agencies to quickly identify persons and vehicles of interest which can help safeguard borders. Many countries already use Jenoptik's advanced technology to combat organised crime and terrorism.
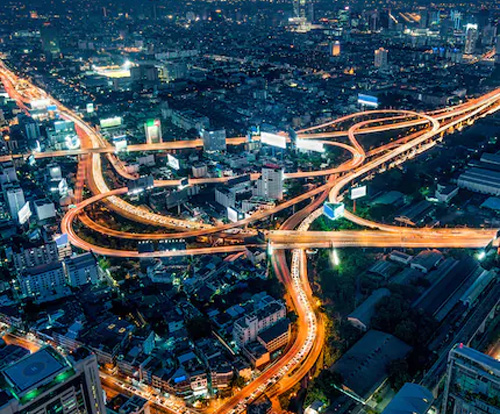
Combating organized crime
- Combat organized crime with ANPR cameras
Record and evaluate ANPR data in real time by using VECTOR² cameras, TraffiData analysis software and TraffiMobile cameras for combating organized crime.
Jenoptik's advanced technologies, products and services help police and security agencies combat organized crime and terrorism. Our experts have years of experience in international projects and will advise you competently on how to effectively increase civil security. Automatic number plate recognition helps to combat organized crime especially at high-risk locations such as connecting roads, city centres, airports and public buildings.
Portable and stationary ANPR cameras and analysis software provide continuous traffic surveillance. VECTOR² cameras are compact, robust and powerful, and can be installed on traffic lights, lighting columns or any other existing masts. Recorded ANPR data is transmitted in real time then processed in a secure data centre. TraffiData analysis software is then used to evaluate the data for comparison against watch lists, instantly alerting the police and security authorities when a suspect vehicle is identified.
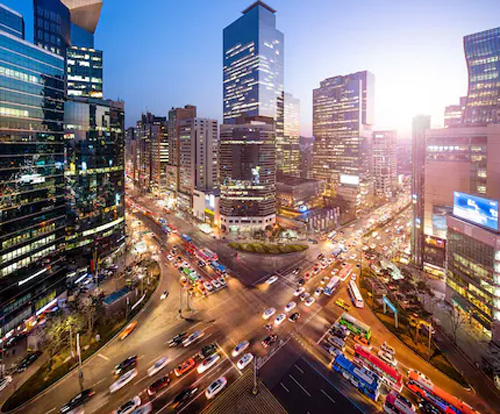
Protecting public places
- ANPR technology helps in the early detection and prevention of organized crime and criminal acts in public places.
Jenoptik's automatic number plate recognition (ANPR) solutions help police and security authorities by increasing security measures in public places. Networks of multiple VECTOR² cameras can be installed for mass surveillances of suspect vehicles approaching highly populated locations such as government buildings, airports, universities, hospitals, shopping malls and multi-story car parks.
VECTOR² cameras have a high capture rate and automatically transmit data to data centres. TraffiData analysis software analyses the information in real time, compares it against police watch lists, and automatically reports suspect vehicles. For example, in a university security zone, a suspect vehicle is detected by the first VECTOR²camera installed in the network. The software reports that this vehicle is within the safety zone. By passing the second VECTOR²camera, police and security officers will know precisely where the car is heading enabling them to take appropriate action.
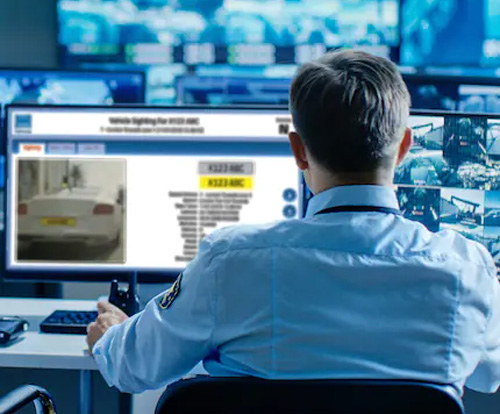
Monitoring suspect vehicles
- Identify, monitor and intercept suspect vehicles
Jenoptik’s automatic number plate recognition (ANPR) enables you to create criminal profiles and movement patterns of suspect vehicles.
Vehicles have a key role in organised crime and are frequently used as a means of transport or escape from criminal activities. ANPR technology helps the police and security authorities to quickly Identify, monitor and intercept suspect vehicles, by enabling crime prevention and increasing civil security.
Powerful ANPR cameras combined with advanced analysis software are designed to filter out suspects from millions of other vehicles. ANPR data is processed and analysed in real time, and the software is able to compare number plates against existing watch lists. When a search returns a hit, like a stolen vehicle or a vehicle with false plates, the police and security authorities are automatically alerted. Filters can then be used to reconstruct movement patterns, departure points and links to other vehicles. Police and security authorities can then create criminal profiles and identify suspect behaviour, enabling them to determine where a suspect vehicle is located, and effectively pursue and prevent crime.