Videos
Loading the player ...
- Offer Profile
- Machines and equipment for the processing of residual materials!
We develop, produce and sell technically sophisticated, high-quality machines and systems for shredding, conveying and processing primary and secondary raw materials in the production and recyclable materials cycle. Thanks to our technically advanced solutions, we are international leaders in the industry. We will accompany you all the way from planning and production to delivery, assembly, commissioning and maintenance. Depending on your requirements, we will supply you with individual machines or complete system solutions – with the highest quality standards worldwide.
Product Portfolio
Shredding
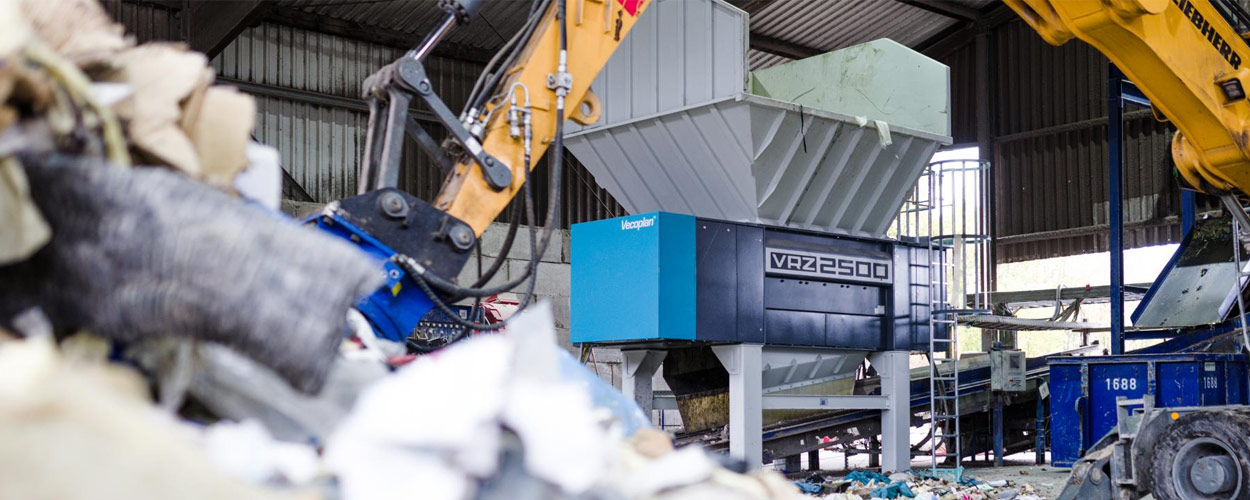
Our core competence in the preparation of residual materials for further processing and recycling
Vecoplan is the market leader for the shredding of residual materials and preparing them for downstream material or thermal processing. We have a wide range of products from which we will select the right machine to perfectly match your specific input material. For example, this applies to a wide variety of plastics, but also to different types of wood. There are also very different types of waste, which are often interspersed with impurities. You can process these waste types for RDF production. We will work closely with you in all your usage scenarios. Our shredders will give you the output that meets your high efficiency and quality requirements.
Single-shaft shredder
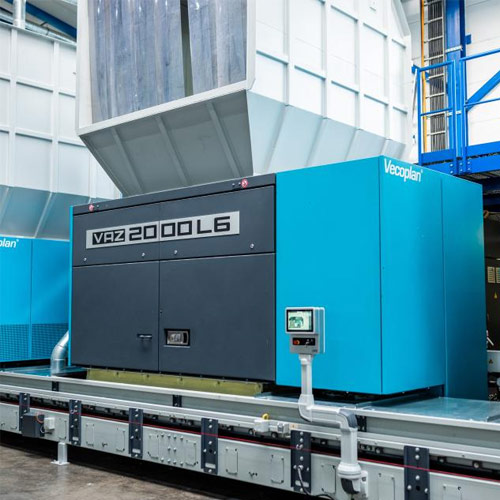
VAZ - Shredder for reusable material
- Robust and sophisticated – the all-rounder among the single-shaft shredders
Robust, powerful and energy-efficient; our high-performance shredders of the VAZ series can be used universally and are the right answer for a wide range of applications. By adapting the rotor design, we aim maximum throughput with homogeneous output, even with challenging materials.
Your advantages at a glance
- Highest reliability and availability
- Energy savings of up to 50 %
- Optimum ease of maintenance
- Maximum homogeneous output with lowest fine dust content
- Best possible value creation thanks to consistent, high-quality output
- Counter knives adjustable from outside the machine
- Supported by the Vecoplan Live Service
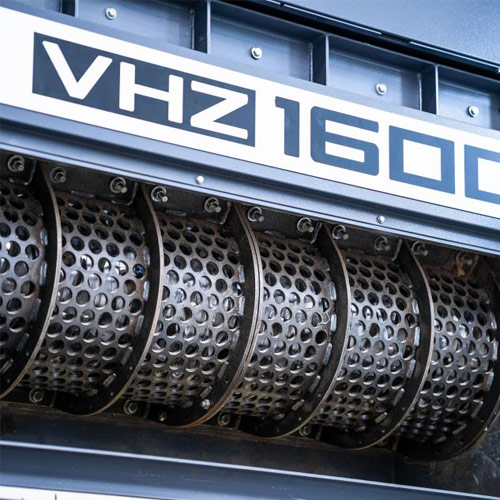
VHZ - Wood shredder
- Energy-efficient shredder for a wide variety of wood waste
Do you want to reliably process chipboard, hardwood and solid wood waste, bark or softwood into wood chips and briquette-ready material? Our VHZ series of compact and robust single-shaft shredders has been specifically designed to master these tasks. You’ll benefit from low operating costs thanks to energy-efficient drive technology, and in most usage scenarios, you can feed the collected materials directly to the machine without the need for additional feeding systems. Since the rotor turns particularly slowly, it makes little noise or dust during vertical feeding.
Your advantages at a glance
- Energy savings of up to 25%
- Tramp material detection
- Highest throughput
- Low maintenance costs
- Simple and fast maintenance
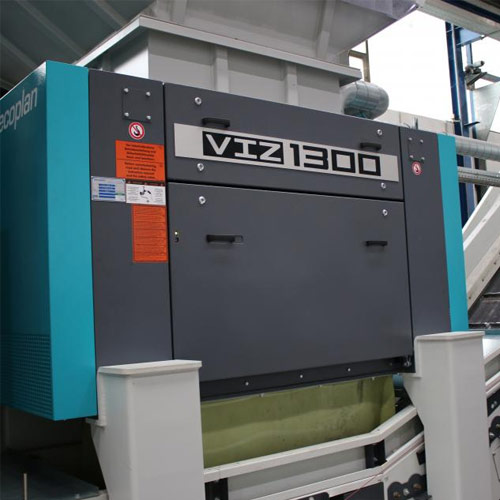
VIZ - High performance shredder
- Infinitely flexible - the ingeniously-adaptable shredding machine for reusable materials
Your challenge is frequently changing material with different requirements? The new Vecoplan shredder offers a correspondingly efficient
and adaptable machine concept in the smallest possible space. Couple this flexibility with low investment and operating costs
and you will experience efficient process stability.
Your advantages at a glance
- Maximum flexibility
- Low investment and operating costs
- Highest availability
- Hardly any losses due to lowest fines content
- Shortest amortisation periods
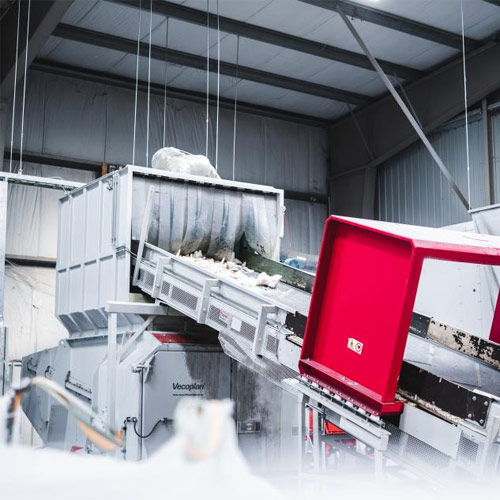
VHD - Heavy duty shredder
- Exceptionally reliable – the shredder for solid materials with the highest mechanical properties
Our VHD is strong in starting and high-torque which are the ideal prerequisites for shredding plastics with the highest mechanical properties.
Almost regardless of geometry and weight, powerfully and reliably on a permanent basis.
Your advantages at a glance
- Millless shredding of solid input materials almost regardless of size and weight
- Maintenance-free synchronous motor as direct drive without mechanical drive train.
- All machine components of particularly solid and stable design
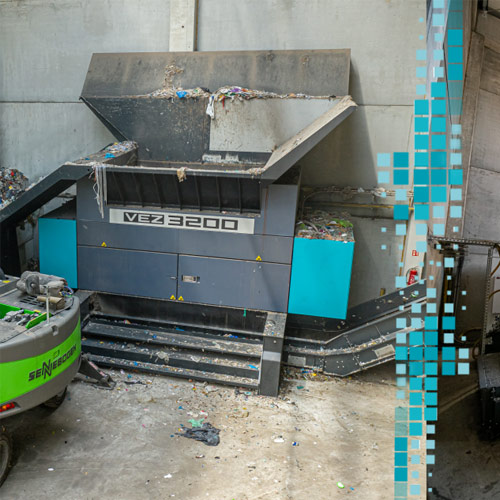
VEZ - RDF shredder
- Extremely tough – pure shredder power in single-stage shredding, of course also in pre- and post-shredding
Equipped with the virtually maintenance-free, proven HiTorc drive, which is absolutely insensitive to contaminants, this dynamic, robust shredder is extremely reliable and powerful, even with the most difficult, contaminant-laden material streams, both in pre-shredding and in single-stage shredding.
You don't have to do without any of these advantages when it comes to secondary shredding.
The secondary shredder is also equipped with state-of-the-art Vecoplan technology.
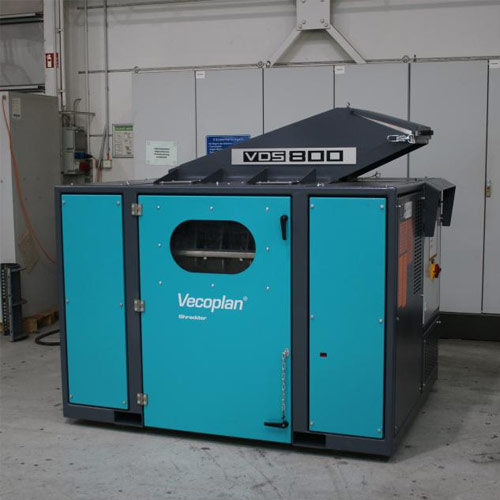
VDS - Data carrier shredding
- It has our trust – the hard disc specialist
By mechanical shredding sensitive data on digital media are destroyed effectively and irreversibly.
The use of different screen sizes allows the implementation of different security levels according to DIN 66399-2.
The shredder can be loaded with charges up to 30 kg. We trust it – trust us.
Your advantages at a glance
- High flexibility thanks to wide area of application
- Simple adjustment thanks to quick screen change
- Low labour costs thanks to batch-by-batch loading
- Ready to plug in, CE-compliant delivery
- Can also be used on a mobile basis
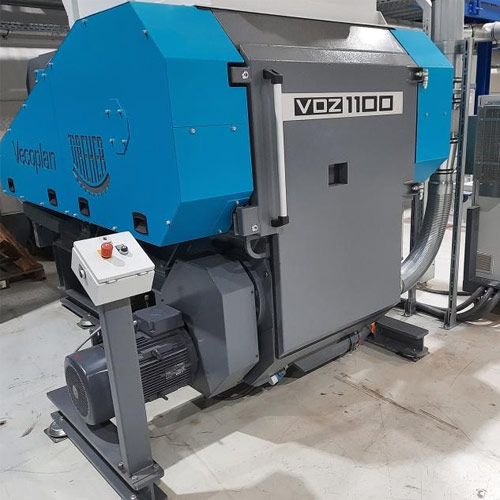
VDZ - Combined shredder-granulator
- 2 in 1 – shredder-mill combination, compact inhouse solution
The intelligent solution is a design jointly developed based cutting mill specialist Heinrich Dreher GmbH & Co. KG from Aachen and Vecoplan AG. It combines the know-how of two German plant and machine manufacturers in one machine housing. The machine crushes the input material in two stages to the desired output grain size for direct reuse in the production flow.
Your advantages at a glance
- 70 % space saving
- 25 % energy savings through ESC-Drive compared to electromechanical direct drive
- Highest reliability and availability
- Safety performance level D2
- Lower connection and consumption costs
Double-shaft shredder
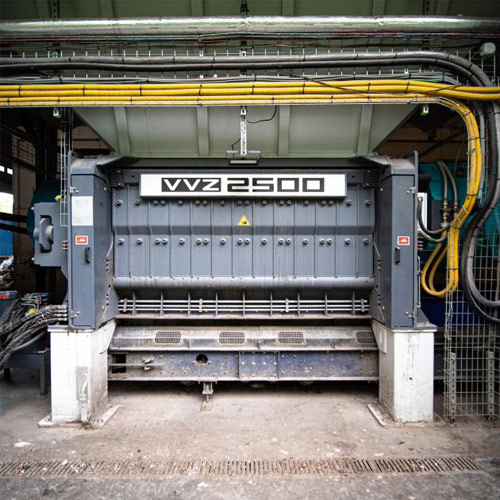
VVZ - Pre-shredder
- Powerful and efficient – twin-shaft shredders for pre-shredding
With the twin-shaft pre-shredder, almost any material can be shredded. The HiTorc drive saves energy and the contaminant detection reduces downtimes.
Maintenance and service costs are minimised by easily replaceable wear parts. The output material is characterised by the best homogenity,
optimally prepared for the next process steps.
Your advantages at a glance
- Robust and durable design for extreme conditions
- Highest reliability and availability
- Cost minimisation through energy efficiency
- Best added value through consistently high, high-quality output
- Intuitive machine operation via VSC.control
- Online support and optimisation via the Vecoplan Smart Center
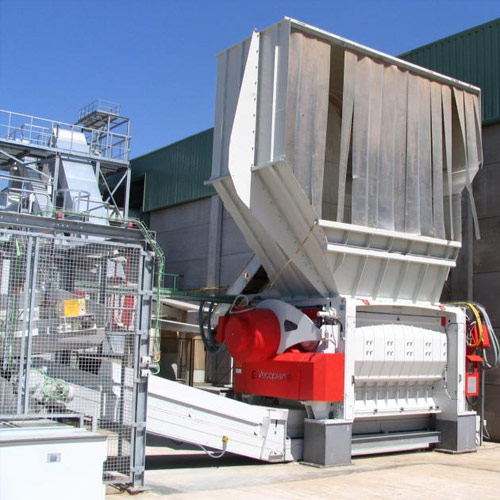
VNZ - Re-shredder
- Re-shredding of prepared demanding residues into separable material
For value and material recovery, you can efficiently process pre-crushed waste wood, pre-shredded domestic waste and even sorting residues into separable material with our VNZ double-shaft re-shredder. We offer different rotor systems and geometries for a varied range of tasks with different materials. We have equipped the VNZ post-shredder with a breakage protection system, which prevents damage to the machine when extraneous materials are present in the materials being fed into it: you can easily remove these materials without having to empty the feeding hopper. You’ll also benefit from low power consumption thanks to the VNZ’s ultra-efficient drive technology.
Your advantages at a glance
- Highest reliability and availability
- Cost minimisation through energy efficiency
- Optimisation of maintenance and service
- Best added value through consistently high, high-quality output
- Support through Vecoplan Live Service
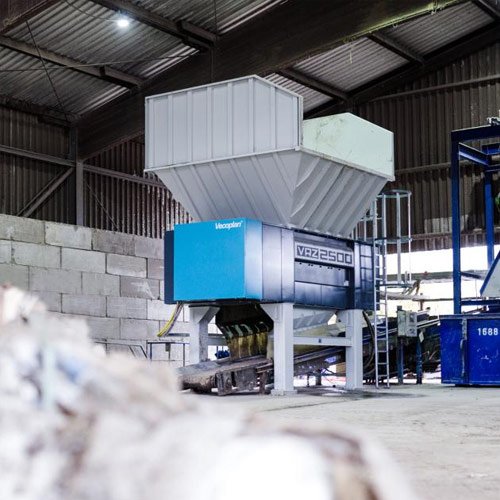
VRZ – Pre-shredder ripping system
- Demanding and reliable – the VRZ seeks the challenge
The VRZ twin-shaft shredder is characterised above all by its rotor: Instead of conventional cutting tools, it is equipped with sickle-shaped ripping teeth. This enables the machine to break up and shred even bulky materials safely. The developers have placed great emphasis on a robust design.
Little maintenance is required - and if it is, it is done quickly.
Your advantages at a glance
- Robust and durable design for extreme conditions
- Highest reliability and availability
- Ergonomic machine design for optimal maintenance and service accessibility
- Increased energy efficiency
- Reduced operating and wear costs
- Intuitive machine operation via VSC. Control
- Online support and optimisation via the Vecoplan Smart Center
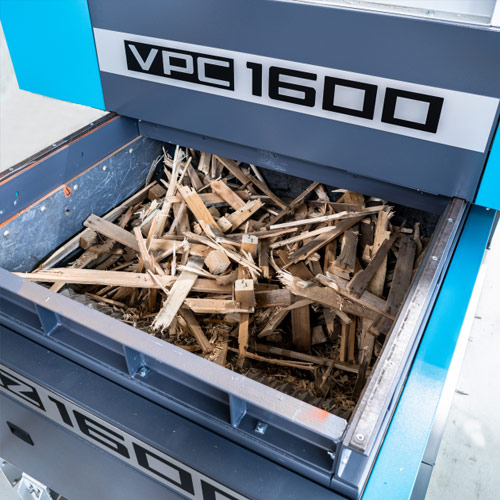
VPC - Pallet crusher
- Pre-shredding of pallets, crates or cable drums made of wood with high throughput.
Do you have to process large-volume and bulky wooden components such as pallets, crates and cable drums – and maintain a high throughput in continuous operation? We can offer you an efficient solution for these jobs – our VPC pallet crusher. Combine this pre-shredder with our VHZ series single-shaft shredder and you’ll increase your throughput by up to 50%! You’ll also save a lot of floor space, which a larger machine would occupy.
Your advantages at a glance
- Increase of the throughput capacity up to 50%
- Low maintenance costs
- Simple and fast maintenance work
- Small space requirement
- Reliable processing of large-volume feed material made of wood
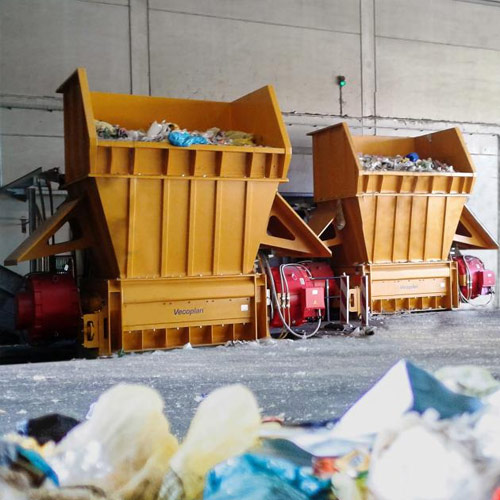
VSA - Bag opener
- Reliably opening and emptying bags, not crushing them - the VSA belongs at the start of a sorting system
With experience and competence, we bundle our knowledge for optimal preparation of well-sortable material for downstream processes.
The bag ripper is excellently equipped and benefits from many well thought-out detailed solutions.
Your advantages at a glance
- Robust and durable design for extreme conditions
- High throughput with very good dosing accuracy
- Highest reliability and availability
- Ergonomic machine design for optimum maintenance and service accessibility
- Increased energy efficiency
- Reduced operating and wear costs
- Intuitive machine operation via VSC. Control
- Online support and optimisation via the Vecoplan Smart Center
Chippers
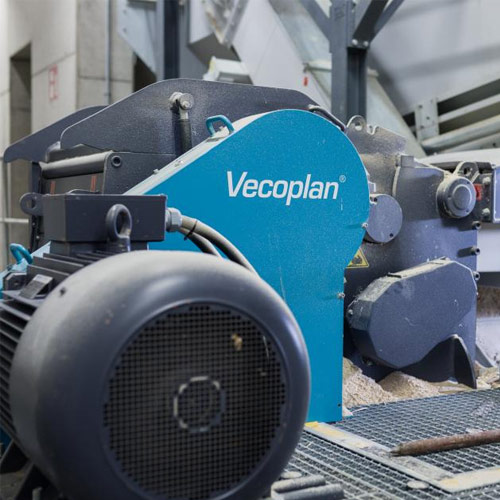
VTH - Drum chipper
- The drum chipper for economical production of wood chips
Do you want to produce fuel chips for energy generation, or quality chips for the cellulose industry – extremely economically? Then look no further than our VTH drum chippers. You’ll achieve enormous throughput rates with these drum chippers. These are stationary machines with a horizontal feeding unit. They are equipped with a rotor fitted with chipping knives for shredding round wood for the energy industry or residual wood in sawmills, for example.
Your advantages at a glance
- Highest reliability and availability
- Low operating costs
- Maximum throughput
- Consistent output quality
- Low losses due to low fines content
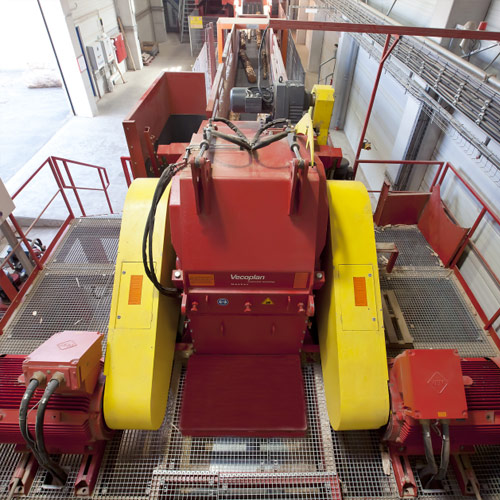
VTH - Biomass chipper
- The solution for the production of wood chips for energy recovery and recycling
Do you prepare wood chips from logs, forest residues and sawmill residues for the pellet industry or as fuels for boiler feed in combined heat and power plants? We can supply you with individually tailored systems with our VTH biomass chippers at their core. Our biomass chipper series covers a very wide performance range in terms of both throughput and the quality of the required output material.
Your advantages at a glance
- Durability and performance
- Extremely compact design
- Easy maintenance
- Optimised infeed
- Optimum price-performance ratio
Pre-shredding
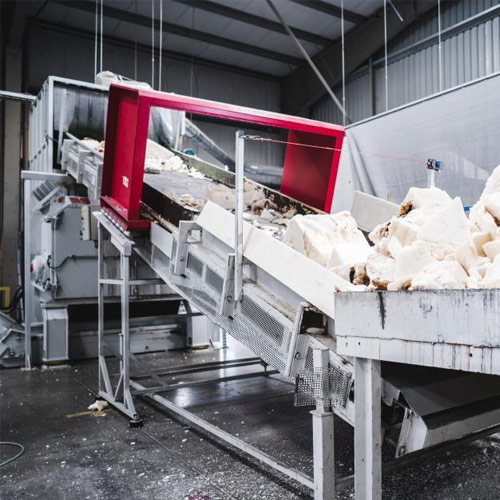
VAZ - Shredder for reusable material
- Great performance in pre-shredding - even with challenging materials
The durable and robust single-shaft shredders of the compact VAZ series are also suitable for the pre-shredding of a wide variety of materials, such as wood, plastics, paper and other recyclables. You can change the initial particle size by means of different screen perforations and thus always obtain a maximum homogeneous output with a low fine dust content for further processing - even with challenging materials.
Your advantages at a glance
- Highest reliability and availability
- Energy savings of up to 50 %
- Optimum ease of maintenance
- Maximum homogeneous output with lowest fine dust content
- Supported by the Vecoplan Live Service
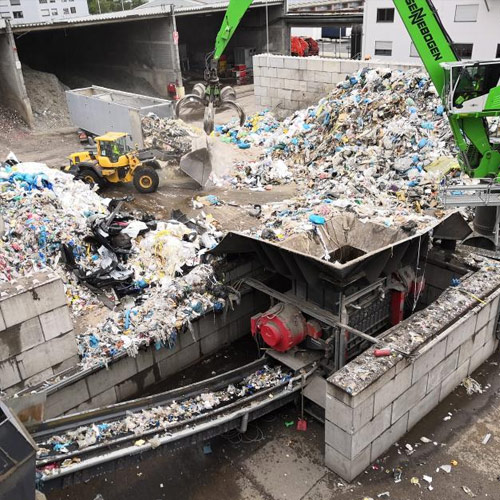
VVZ - Pre-shredder
- Robust and powerful pre-shredding, even of difficult materials
With our VVZ series, you get robust and powerful pre-shredders that can easily pre-shred even difficult and contaminated material, such as household, bulky and commercial waste, production residues or waste wood, straw and root wood for further processing. Two solid steel rotors with their large flywheel masses achieve smooth machine operation and high penetrating power. Due to the interaction of the two rotors with the common counter knife and the screen webs, you benefit from a very well separable and homogeneous output.
Your advantages at a glance
- Robust and durable design for extreme conditions
- Highest reliability and availability
- Cost minimisation through energy efficiency
- Best added value through consistently high, high-quality output
- Intuitive machine operation via VSC.control
- Online support and optimisation via the Vecoplan Smart Center
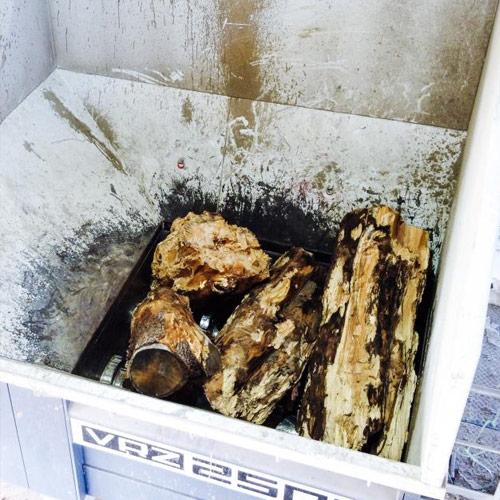
VRZ – Pre-shredder ripping system
- Successful pre-shredding even for bulky materials
Our VRZ is ideally suited for the pre-shredding of a wide variety of materials. By using sickle-shaped ripping teeth instead of conventional cutting tools, the machine can easily break up even difficult or bulky materials and thus prepare them for further processing. Thanks to its robust design, you can use the pre-shredder without interruptions over a long period of time - at low operating costs and low maintenance.
Your advantages at a glance
- Robust and durable design for extreme conditions
- Highest reliability and availability
- Ergonomic machine design for optimal maintenance and service accessibility
- Increased energy efficiency
- Reduced operating and wear costs
- Intuitive machine operation via VSC. Control
- Online support and optimisation via the Vecoplan Smart Center
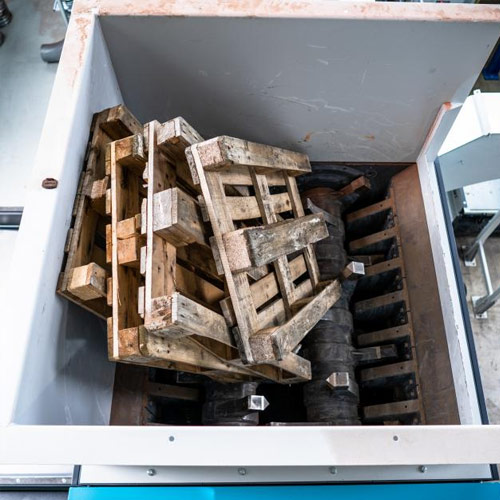
VPC - Pallet crusher
- Optimal pre-shredding of large-volume and bulky components made of wood
For the pre-shredding of large-volume and bulky components such as boxes and pallets made of wood, we have developed the Vecoplan Pallet Crusher VPC 1600. This can be combined with the single-shaft shredder VHZ 1600, which then processes the pre-shredded material directly into homogeneous wood chips or briquette-ready material. This allows you to increase throughput by up to 50 percent. The special feature: In the VPC, the material is not cut, but crushed. This creates enormous advantages in the pre-shredding process and reduces the quantities of wear parts.
Your advantages at a glance
- Increase of the throughput capacity up to 50%
- Low maintenance costs
- Simple and fast maintenance work
- Small space requirement
- Reliable processing of large-volume feed material made of wood
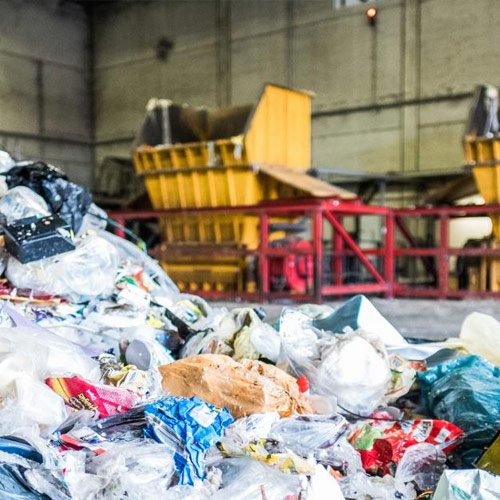
VSA - Bag opener
- For the gentle pre-shredding of recyclable materials
Our VSA (Vecoplan Bag Opener) as a pre-shredder gently opens yellow bags and empties them carefully without shredding their contents. Since the system only breaks the materials, this simplifies the subsequent sorting out of the valuable, recyclable materials. The sales packaging made of different materials or even household waste collected in the bags can thus be continuously and reliably fed to further processing and thus be recycled efficiently. This provides downstream processes with a material that can be easily sorted.
Your advantages at a glance
- Robust and durable design for extreme conditions
- High throughput with very good dosing accuracy
- Highest reliability and availability
- Ergonomic machine design for optimum maintenance and service accessibility
- Increased energy efficiency
- Reduced operating and wear costs
- Intuitive machine operation via VSC. Control
- Online support and optimisation via the Vecoplan Smart Center
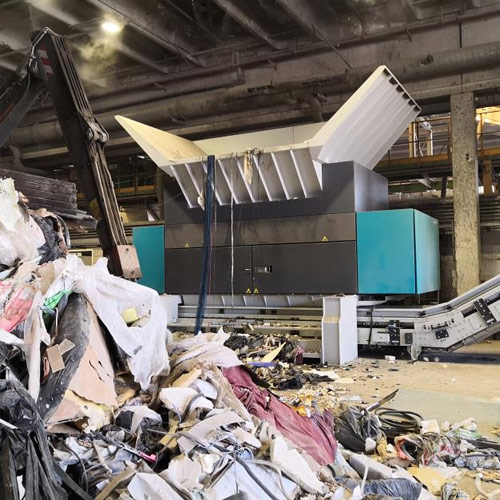
VEZ - RDF shredder (pre-shredding)
- Pre-shredding of a wide variety of input materials for the production of substitute fuels
Alternative fuels recovered from production and sorting residues, packaging material and domestic and commercial waste have proven to be a cost-effective solution for providing energy in cement and power plants. Our VEZ-TV and VEZ-TTV pre-shredders are equipped with one and two HiTorc drives respectively, and these machines can efficiently process a wide range of totally different input materials. You can integrate these two robust shredders into your existing processes and shredding lines or set up a completely new processing system. The result is a totally reliable process with a consistently high output quality.
Your advantages at a glance
- Robust and durable design for extreme conditions
- Unlimited flexibility through various configuration options
- Highest reliability and availability
- Cost minimisation through energy efficiency
- Ergonomic machine design for optimum maintenance and service accessibility
- Best added value through consistently high and homogeneous output
- Intuitive machine operation via VSC. Control
- Online support and optimisation via the Vecoplan Smart Center
Re-shredding
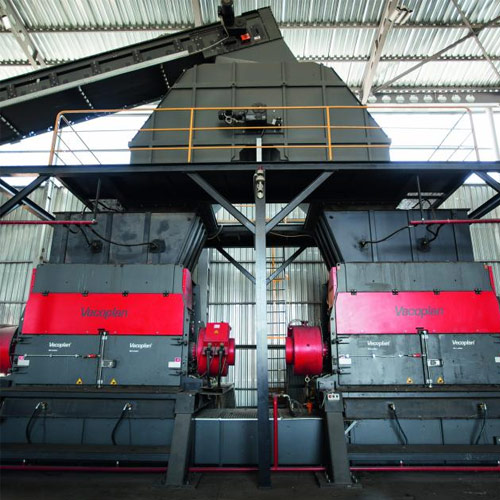
VEZ - RDF shredder (re-shredding)
- Series specially designed for the secondary shredding of domestic and commercial waste in the production of substitute fuels
A constantly high level of output quality is essential if materials such as production and sorting residues, packaging material and domestic and commercial waste are to be efficiently converted into energy in cement and power plants. The Vecoplan VEZ-T series and the VEZ-TT series with one and two HiTorc drives respectively are re-shredders designed to master these challenging tasks. Your production will benefit from a consistently secure process.
Your advantages at a glance
- Robust and durable design for extreme conditions
- Unlimited flexibility through various configuration options
- Highest reliability and availability
- Cost minimisation through energy efficiency
- Ergonomic machine design for optimum maintenance and service accessibility
- Best added value through consistently high and homogeneous output
- Intuitive machine operation via VSC. Control
- Online support and optimisation via the Vecoplan Smart Center
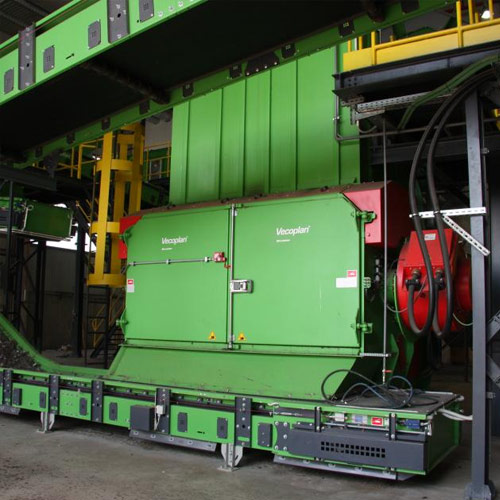
VAZ - Shredder for reusable material
- Efficient re-shredding in material processing
The Vecoplan VAZ shredder for reusable materials is designed for a wide range of applications. Due to its equipment options and resulting throughput capacity, you can also use it for re-shredding in material preparation, for example in thermal recycling. By minimizing overlengths, you achieve a significant improvement in material quality, which is often a mandatory requirement for downstream processes.
Your advantages at a glance
- Highest reliability and availability
- Energy savings of up to 50 %
- Optimum ease of maintenance
- Maximum homogeneous output with lowest fine dust content
- Supported by the Vecoplan Live Service
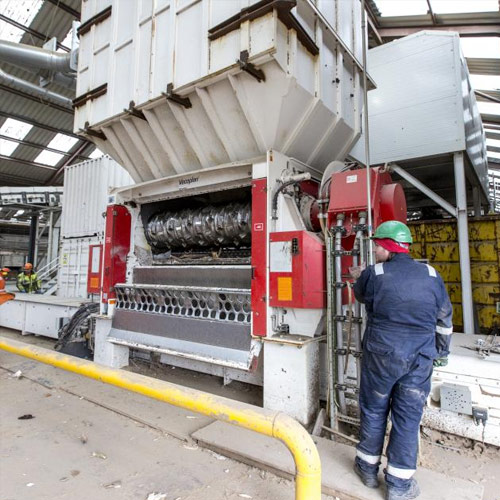
VNZ - Re-shredder
- Powerful re-shredding of pre-crushed material
With our VNZ series, you get high-performance secondary shredders in a robust design, which have been specially developed for the re-shredding of pre-crushed material to produce separable material for value and material use. Waste wood, pre-shredded domestic, industrial and commercial waste, production waste, straw, root wood and much more can be processed without any problems. Various rotor systems and geometries are available for optimum shredding performance with different material tasks.
Your advantages at a glance
- Highest reliability and availability
- Cost minimisation through energy efficiency
- Optimisation of maintenance and service
- Best added value through consistently high, high-quality output
- Support through Vecoplan Live Service
Dissolving / opening of packagings
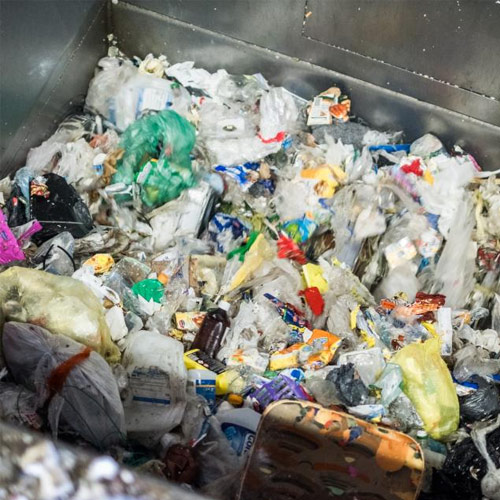
VSA - Bag opener
- For the gentle dissolving and careful opening of refuse sacks
With the VSA (Vecoplan Bag Opener), we have developed a robust, low-maintenance and extremely energy-efficient bag opener with a high throughput rate that allows you to gently open and empty yellow bags. The special design allows the bags to be carefully torn without shredding their contents. Even bag-in-bag fractions, which are common during yellow bag collections, can be guaranteed by this operation, allowing more materials to be recycled.
Your advantages at a glance
- Robust and durable design for extreme conditions
- High throughput with very good dosing accuracy
- Highest reliability and availability
- Ergonomic machine design for optimum maintenance and service accessibility
- Increased energy efficiency
- Reduced operating and wear costs
- Intuitive machine operation via VSC. Control
- Online support and optimisation via the Vecoplan Smart Center
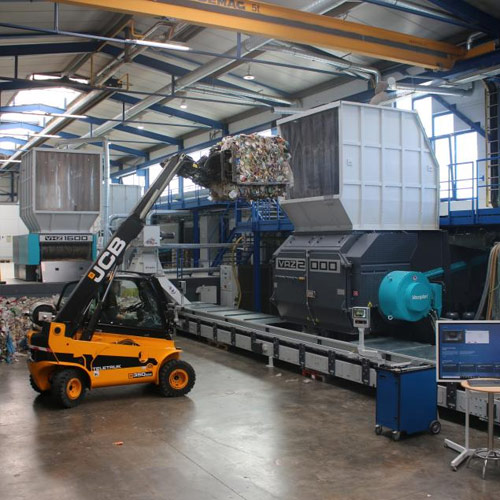
VAZ - Shredder for reusable material
- Problem-free shredding even of complete bales
The VAZ shredder for reusable materials is generally used for single-stage shredding or pre- or re-shredding of a wide variety of input materials. The larger types of this proven series are even suitable for those applications where complete packages have to be broken up or opened and crushed. For example, you can feed the baled material directly through the hopper. The shredders handle this task without any problems.
Your advantages at a glance
- Highest reliability and availability
- Energy savings of up to 50 %
- Optimum ease of maintenance
- Maximum homogeneous output with lowest fine dust content
- Supported by the Vecoplan Live Service
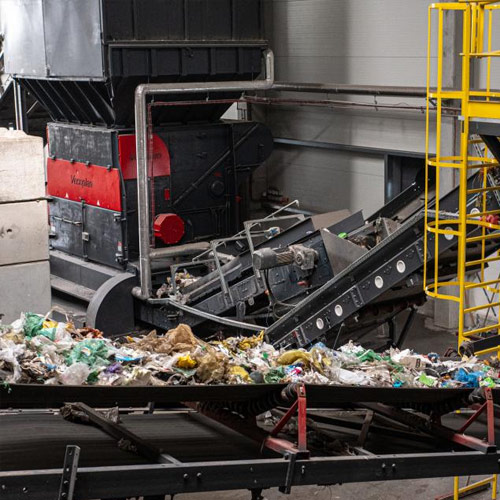
VEZ - RDF shredder
- The larger construction types can also be used to dissolve, open and crush containers without any problems
The Vecoplan VEZ RDF shredder is generally used for single-stage shredding or pre- or re-shredding. The larger types of this proven series are also suitable for applications where complete bales have to be broken up or opened and shredded. For example, you can feed the baled material directly through the hoppe
Your advantages at a glance
- Robust and durable design for extreme conditions
- Unlimited flexibility through various configuration options
- Highest reliability and availability
- Cost minimisation through energy efficiency
- Ergonomic machine design for optimum maintenance and service accessibility
- Best added value through consistently high and homogeneous output
- Intuitive machine operation via VSC. Control
- Online support and optimisation via the Vecoplan Smart Center
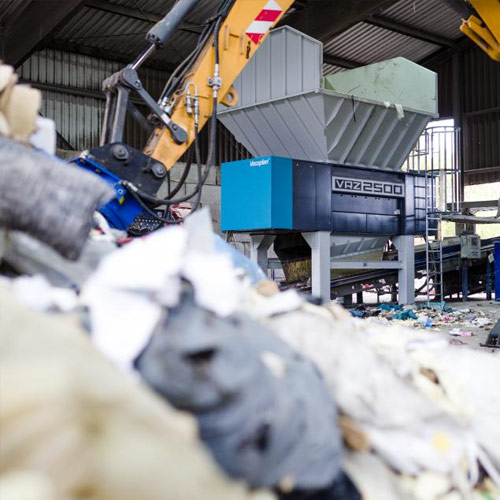
VRZ – Pre-shredder ripping system
- Demanding and reliable – the VRZ seeks the challenge
The VRZ twin-shaft shredder is characterised above all by its rotor: Instead of conventional cutting tools, it is equipped with sickle-shaped ripping teeth. This enables the machine to break up and shred even bulky materials safely. The developers have placed great emphasis on a robust design.
Little maintenance is required - and if it is, it is done quickly.
Your advantages at a glance
- Robust and durable design for extreme conditions
- Highest reliability and availability
- Ergonomic machine design for optimal maintenance and service accessibility
- Increased energy efficiency
- Reduced operating and wear costs
- Intuitive machine operation via VSC. Control
- Online support and optimisation via the Vecoplan Smart Center
Single-stage RDF shredding
VEZ - RDF shredder
- For single-stage RDF production
The Vecoplan VEZ RDF shredder can be used variably: In single-stage shredding, it is used for the production of sortable and conveyable material for refuse-derived fuel generation from production residues for the production of a grain size of up to
Your advantages at a glance
- Robust and durable design for extreme conditions
- Unlimited flexibility through various configuration options
- Highest reliability and availability
- Cost minimisation through energy efficiency
- Ergonomic machine design for optimum maintenance and service accessibility
- Best added value through consistently high and homogeneous output
- Intuitive machine operation via VSC. Control
- Online support and optimisation via the Vecoplan Smart Center
Two-stage plastic shredding
VDZ - Combined shredder-granulator
- Shredding and grinding in one machine
With our VDZ combined shredder & granulator, you can shred input material such as purgings and bulky components to the desired output particle size in two stages. The regranulate can then flow back into the production stream. The key feature here is that we have combined the pre-shredding and granulating steps in one compact machine. This eliminates the need for conveyors and other transport systems and will save up to 70% space in your plant. The connected load and power consumption are also lower than in two-stage shredding with a conveyor belt. You also have fewer interfaces.
Your advantages at a glance
- 70 % space saving
- 25 % energy savings through ESC-Drive compared to electromechanical direct drive
- Highest reliability and availability
- Safety performance level D2
- Lower connection and consumption costs
Data carrier shredding
VDS - Data carrier shredding
- Shredding different types of data carriers into the required particle sizes using different sieve sizes
Do you want to destroy sensitive data effectively and irreversibly? We’ve designed our VDS series to master this task. These machines mechanically shred hard disks and other magnetic or optical data carriers such as tapes or CDs. Different particle sizes can be set via different screen sizes to meet the required security levels. A lockable feed chute delivers the materials to the machine. Batches of up to 30 kg can be fed to the machine – and you’ll also benefit from quiet operation thanks to the machine’s encapsulated design.
Your advantages at a glance
- High flexibility thanks to wide area of application
- Simple adjustment thanks to quick screen change
- Low labour costs thanks to batch-by-batch loading
- Ready to plug in, CE-compliant delivery
- Can also be used on a mobile basis
Conveying
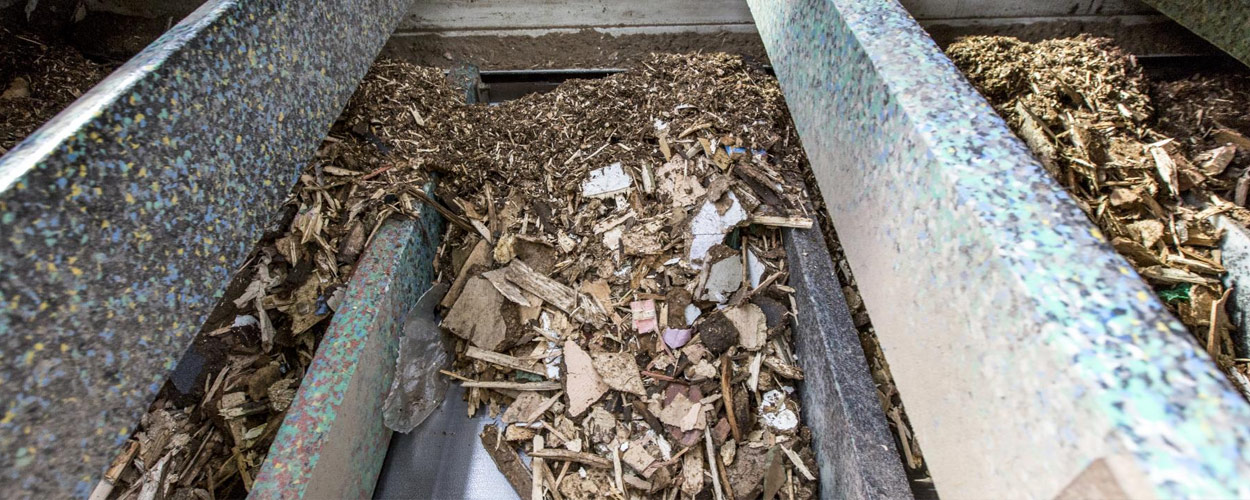
The important link between the single process steps in your processing plant
Vecoplan has solutions for conveying technology in its programme – and they are suitable for all types of bulk materials. We’ll tailor the modular systems to your processes in terms of size, length and performance and we’ll also coordinate the individual components down to the last detail. This means that material flows in your recycling and processing plant will run continuously, and they’ll be reliably fed to the right process steps as well – a major contribution to the high overall economic efficiency of your system.Belt conveyor
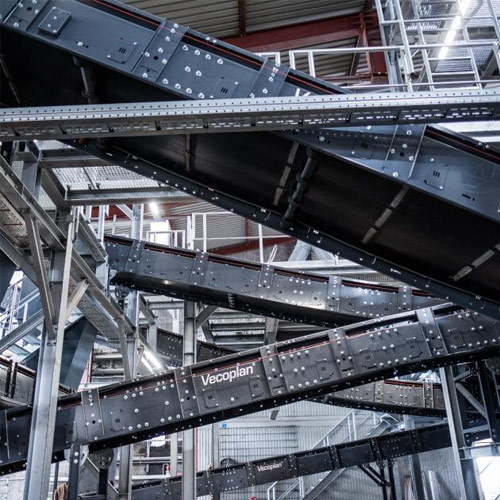
VFB – Conveyor belt
- The Vecoplan conveyor belt impresses with its versatility, which allows it to be used with a wide range of materials
With our flat and trough belt conveyors of the VFB series, you get continuous conveyors of modular design with which you can transport various bulk materials safely. With a particularly resistant oil- and grease-resistant rubber belt, designed for maximum conveying capacity in continuous operation and the option of installing various belt cleaning, safety and monitoring systems, the Vecoplan flat- / trough belt conveyor is ideally suited for transporting a wide range of materials such as wood, biomass, waste, metals, plastics, substitute fuels, etc.
Your advantages at a glance
- Robust and modular design with over 50 years of experience
- Modern and efficient scraper technology
- Banana design can be designed in rising or falling form
- Flat or moulded belt construction
- Lower belt / upper belt covering available
- Anti-magnetic design possible
- Side sealing as standard
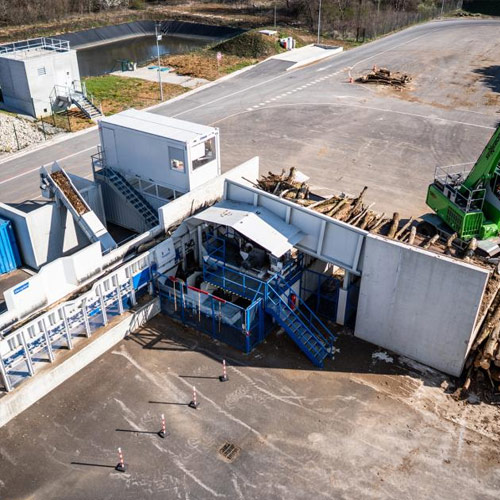
VHB – Chipper feeding conveyor
- Safe and robust feeding of even massive logs into the chipper
The Vecoplan drum chipper feeding conveyor is designed for the horizontal feeding of wood trunks into a drum chipper. The solid welded construction with the generously designed support rollers and the conveying belt specially designed for this application ensure the high availability. This conveyor has a reinforced feeding area adapted to the length of the logs, on which the logs to be chipped can be fed by means of an upstream chain cross conveyor or by means of a log gripper.
Your advantages at a glance
- very solid tub construction with profile steel reinforcement
- special damping elements in the feeding area
- shock absorbing support rollers
- integrated metal-free zone for the use of metal detectors
- optionally: stable baffle wall opposite the feed side V-shaped flared trough for crane removal of contaminated wood
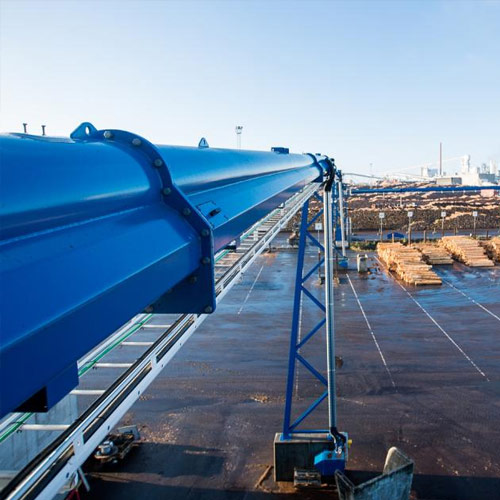
VRF - Pipe conveyor
- The Vecoplan pipe belt conveyor system enables clean and quiet transport over long distances
With the VRF series of pipe belt conveyors, we offer a transport system for almost all types of bulk materials.
In various designs and pipe diameters, materials such as substitute fuel from industrial waste or used tyres, biomass or even sawdust can be transported very efficiently and quietly. High availability is always at the centre of the solution.The special advantage: the conveyors are particularly good at bridging long distances and also cope with inclines without any problems. The use of an air cushion underneath the conveyor belt reduces the friction to a minimum and enables an extremely high conveying capacity with very low drive power.
Your advantages at a glance
- Developed for the efficient conveying of bulk materials over long distances
- Conveying distances of more than 450 m in one operation are possible
- Support distances up to max. 75 m
- Specific drive power approx. 1 kW/10 m (depending on material, conveying capacity and incline)
- Low-noise and low-dust conveying due to a belt run in a closed tube
- Simple pre-assembly on the ground
- No foot traffic concept required
Chain conveyor
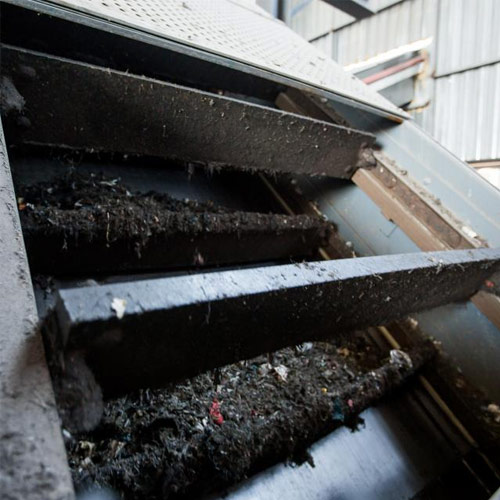
VKU - Chain conveyor with lower belt conveying
- The Vecoplan chain conveyors offer different possibilities for material transport
Our Vecoplan drag chain conveyor type VKU is a modular continuous conveyor for bulk transport. Depending on the design, the material is conveyed by one or two endless conveyor chains with feed dogs on the trough bottom. The chain returns happens above on low-wear and maintenance-free chain guide rails. The compact, closed, self-supporting construction ensures low-wear transportation for large spans.
Your advantages at a glance
- low space requirement, large climbing angles possible
- closed system, thus operationally safe and low dust
- feeding possible at any point. Unloading can be freely selected by mounting motorized or pneumatic ram.
- energy efficient conveying
- low maintenance
- simple, compact and robust design
- high availability
- easily replacable wear parts due to screwed design
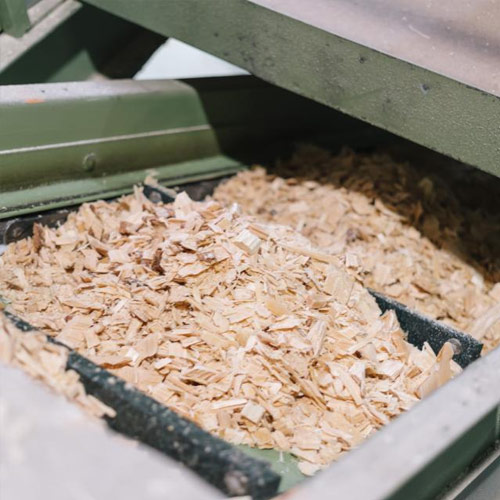
VKO - Chain conveyor with upper belt conveying
- Vecoplan upper trum conveyros type VKO transport your bulk materials trouble-free, even with excess lengths
The Vecoplan drag chain conveyor type VKO - 2 is a modular continuous conveyor for bulk transport, especially for bulk with large particle sizes or as evacuation conveyor. The conveying material is transported in the trough bottom by two endless running conveying chains with feed dogs. The chain return happens
below the conveying trough on low-wear and maintenance-free chain guide rails. The compact, self-supporting construction ensures low-wear transportation for large spans.
Your advantages at a glance
- This type of drag chain conveyor is particularly suitable as a discharge conveyor, e.g. after discharge silos such as push / pull floors or loading and unloading conveyors.
- insensitive to overlenghts and impurities
- low space requirement, large climbing angles possible
- feeding possible at any point.
- energy efficient conveying
- low maintenance requirements
- simple, compact and robust design
- high availability
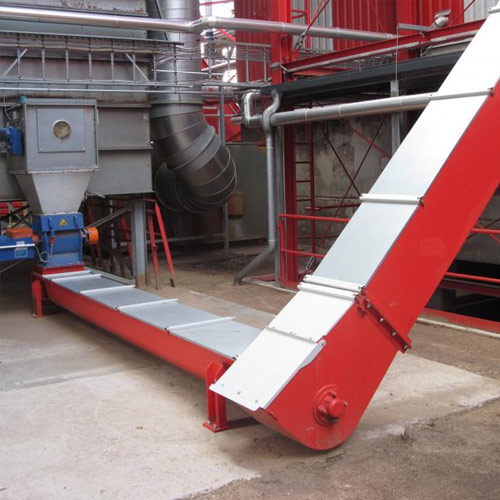
VKS – Chain conveyor with screw
- Two proven systems have been combined for optimum removal after the shredding process
The solution for compact and space-saving removal of bulk materials. Specially developed for the disposal of shredders or for continuous material removal. The VKS series combines the effects of a screw chain conveyor with those of a chain conveyor, in a space-saving manner and usually with one drive. The series is available in trough widths of 300, 400 and 500 millimetres and with screw diameters of 180, 250 and 315 millimetres.
Your advantages at a glance
- Compact system, worm and chain conveyors can be equipped with one drive
- Can be used as a discharge conveyor for a wide variety of storage systems
- Space-saving solution for the disposal of shredding machines
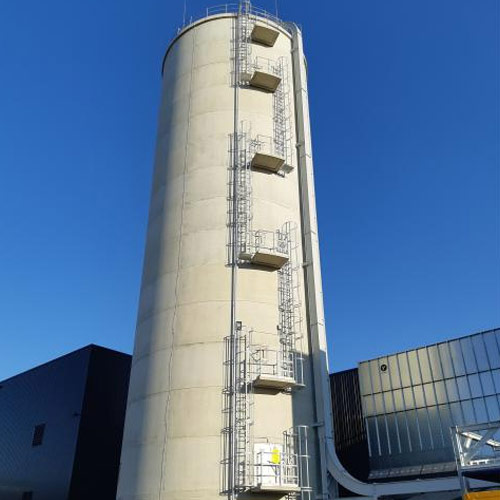
VKV – Vertical chain conveyor
- There is also a solution for vertical transport in the Vecoplan product range
Do you need a conveying solution with which you can convey bulk material vertically - for example into a silo? For this task, we we offer you the VKV vertical chain conveyor. We adapt the conveyor and the equipment of the system to your material flow.
You benefit from robust technology with low maintenance and high availability.
Your advantages at a glance
- Adaptation of the conveyors and the equipment of the system to your material flow
- Vertical conveying
- Robust technology
- Low maintenance
- High availability
Screw conveyor
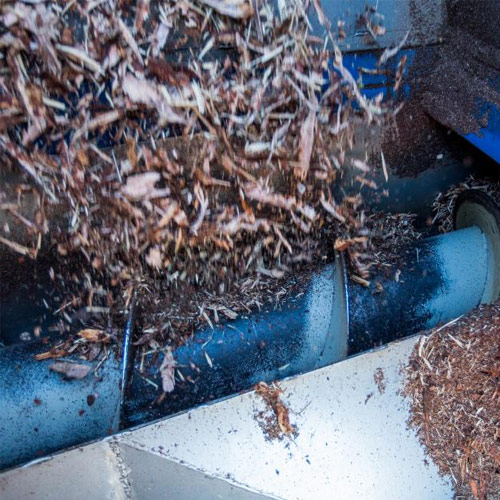
VSE - Single screw conveyor
- For metered and uniform conveying, the single-shaft screw conveyors are ideally suited due to their perfect flow behaviour
Single-shaft screw conveyors are ideal for bulk materials that flow well. The single-screw Vecoplan conveyors can convey bulk materials as well as granular, small-sized, and even semi-moist and fibrous materials, transporting them all finely dosed and uniformly. The conveyance route can be both horizontal and ascending. Depending on the delivery diameter, you will achieve delivery rates of five to 750 cubic metres per hour. We have designed the units to be compact and robust. They can be loaded and unloaded at any point. The screw conveyors offer long service life and low maintenance.
Your advantages at a glance
- Simple, compact and robust design
- Individual loading possibilities of the conveyed material at any position
- Material selection and wear lining individually according to requirements
- Long lifetime, low maintenance
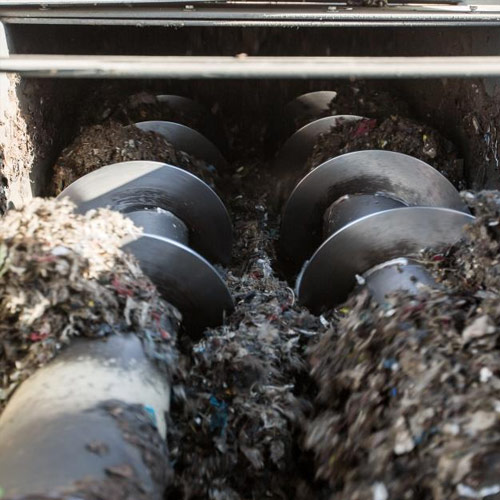
VSD - Double screw conveyor
- Vecoplan offers the double screw conveyor to convey powdery, difficult-flowing bulk materials that tend to form bridges in a metered and uniform manner.
Double screw conveyors are preferred for powdery, stubbornly flowing bulk materials that tend to form “bridges”. Vecoplan’s double screw conveyors of the VSD series convey materials like this in a dosed and uniform manner. The conveyance route can be both horizontal and ascending. The design is single-shaft or multi-shaft depending on the usage scenario. Pumping capacity is up to 700 cubic metres per hour (depending on the pumping diameter). You will benefit from a simple, compact and robust design, a long service life and low maintenance.
Your advantages at a glance
- Depending on the conveying diameter, a conveying capacity of up to 700 cubic meters per hour is achieve
- Individual loading possibilities of the conveyed material at any point
- Simple, compact and robust design
- High lifetime, low maintenance
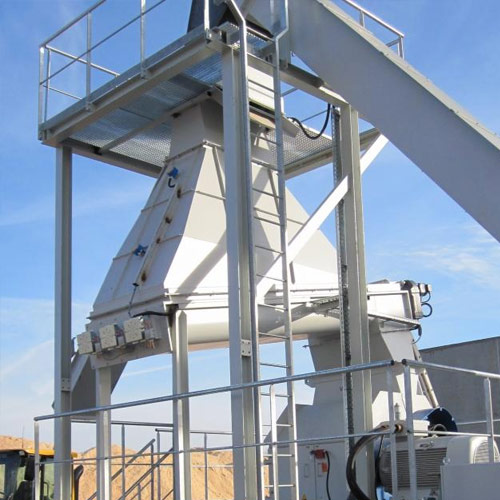
VSM - Screw discharger
- Discharge of bulk material with uniform volume flow and high conveying capacity
With our VSM series screw dischargers, you can economically discharge very different bulk materials such as wood chips, sawdust, or even biomass from silos and bins continuously - even with difficult materials. The VSM series also prevents bridging and segregation of the material. Thanks to the modular components, you can use our discharge trays in a variety of ways.
Your advantages at a glance
- Prevention of bridging and segregation of the material
- Versatile use thanks to modular components
- High conveying capacity and even volume flow
- Long lifetime, low maintenance requirements
Supply of bulk material
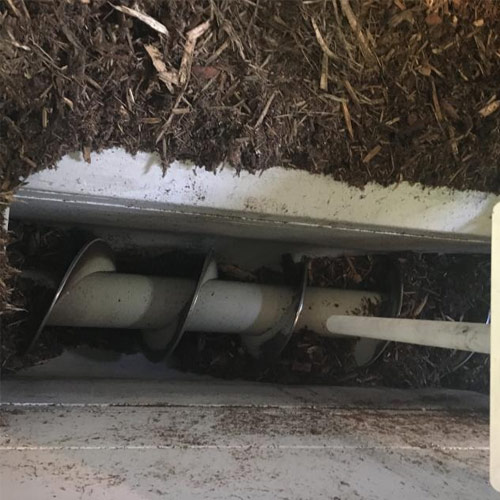
VSE - Single screw conveyor
- For the metered and uniform conveying of bulk materials
For bulk material feeding, Vecoplan has the single screw conveyors of the VSE series in its program. These are particularly suitable for bulk materials with good flow characteristics. The course can be either horizontal or ascending. Depending on the conveying diameter, they have a conveying capacity of five to 750 cubic meters per hour. The screw conveyors offer long service lives and low maintenance requirements.
Your advantages at a glance
- Simple, compact and robust design
- Individual loading possibilities of the conveyed material at any position
- Material selection and wear lining individually according to requirements
- Long lifetime, low maintenance

VSD - Double screw conveyor
- A metered and uniform feeding of bulk materials
Vecoplan has developed the VSD double screw conveyor for the metered and uniform feeding of bulk materials, preferably for powdery, heavy-flowing bulk materials with a tendency to bridge. The course can be either horizontal or ascending. Depending on the application, the design is single- or multi-flute. Depending on the conveying diameter, you get a conveying capacity of up to 700 cubic meters per hour. In addition, you benefit from a simple, compact and robust design as well as a long service life and low maintenance requirements.
Your advantages at a glance
- Depending on the conveying diameter, a conveying capacity of up to 700 cubic meters per hour is achieve
- Individual loading possibilities of the conveyed material at any point
- Simple, compact and robust design
- High lifetime, low maintenance
Vibration conveyor
VVR - Vibrating conveyor
- Vibrating conveyor are suitable for feeding of drum chipper or also for discharge of bulk material
Vibration conveyors feed residual wood to the drum chippers in sawmills. They can also be used for the transport of bulk materials such als fuels (wood chips) in a boiler charging system. If required, we can equip the systems with contaminant detection and an integrated screening zone. Vibration conveyors compensate for volume fluctiations in the feeding and feed the material evenly and continuously to the downstream process.
Your advantages at a glance
- High conveying capacity
- Low-maintenance continuous operation
- Easy and quick to clean
- Gentle and even conveying
- Solid construction
Storing and Dosing
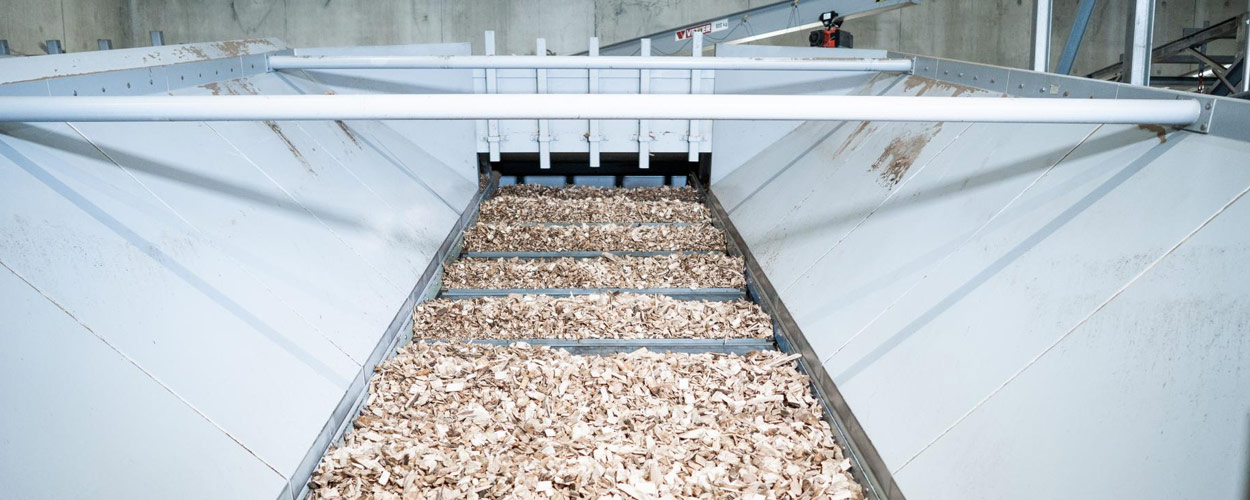
Systems for reliable and continuous material availability in large residual material processing and recycling plants
We offer solutions to receive, feed, convey & store bulk materials and prepare them for further processing. We will supply you with systems that are precisely tailored to your requirements. We use various product and system solutions to ensure that your material is fed consistently and with reliable dosing. We match these solutions 100% to your processes and your individual process steps. Our individual components for storage and dosing will increase your material availability and secure & accelerate the material flow.Bulk material storage
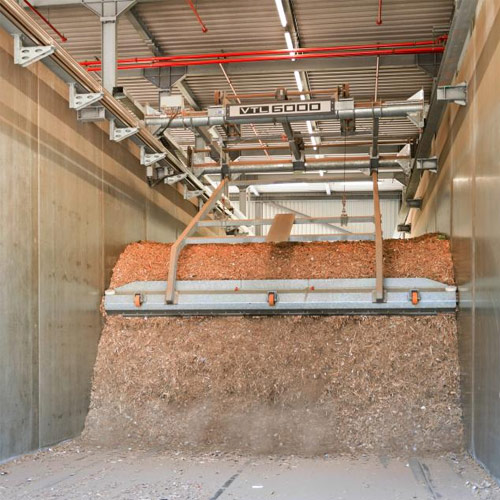
VTL - Toploader
- The most economical storage technology for various bulk materials like wood chips, old timber, bark, RDF, corn, grass and plastic
With our VTL Toploader system, you can store bulk material fully automatically and discharge it in a metered manner. You can use our toploader, for example, to feed the boilers in biomass power plants, as a truck receiving station, as storage boxes for chips and shavings in pellet plants or for substrate storage.
Your advantages at a glance
- Easy and efficient storage technology for small to medium quantities of bulk materials such as wood chips and waste wood
- Ideal for boiler feeding in biomass power plants
- Fully automatic box evacuation without operating personnel
- Filling one or more boxes (up to 400 m³ each) using a semi-trailer, tipping scrap skips or wheel loader on even ground
- Discharge capacities of up to 100 m³/h
- Drive, lifting device, mechanical devices are outside of the bulk material and always easy to maintain
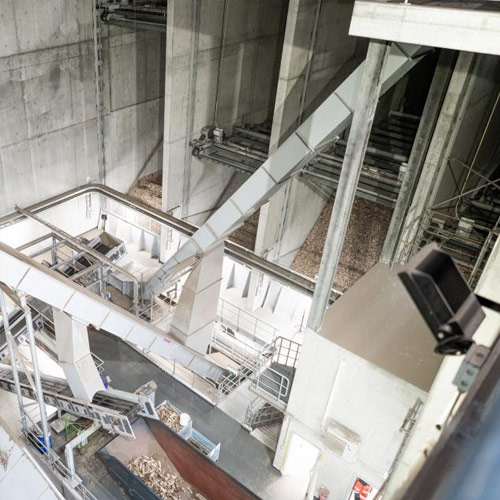
VBE - Loading and unloading conveyors
- Widely used system for the fully automatic storage of bulk materials
With our VBE loading and unloading conveyor, you can economically fill and empty one or more storage boxes with widths of five metres and lengths of up to around 30 metres – even simultaneously if required. The bulk material, such as wood chips, is filled fully automatically, distributed in the box and discharged in a metered manner. If several boxes are used, different bulk materials can even be mixed.
Your advantages at a glance
- High storage volume in a small area Storage mechanism is arranged above the material
- Simultaneous material infeed and discharge is possible
- Mixing of different materials is possible
- Fully automatic storage system
- Modular construction
- The boxes can be erected in concrete, steel or wooden construction
Discharge of bulk material
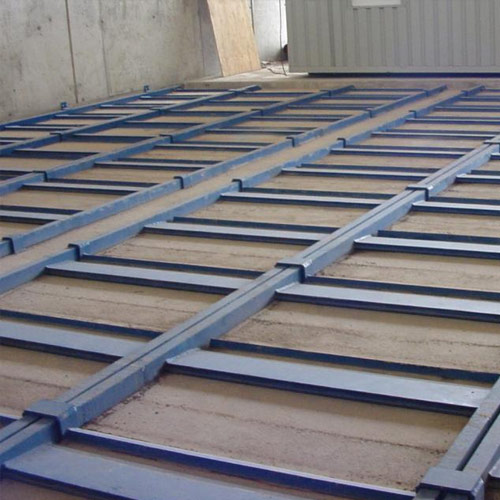
VDB, VZB – Hydraulic discharge device (pushing cylinders)
- The Vecoplan traction pull rod dischargers are specially designed for high discharge capacities
Do you need a pull rod discharger to discharge bulk material such as wood chips, sawdust, RDF, shredded film and plastics from your silo, deep bunker or storage boxes? Our VDB and VZB series are efficient systems with high performance. Each drive unit works independently with its own control system and optional energy-efficient frequency converter.
Your advantages at a glance
- Available as standard version (VZB) or delta version (VDB)
- Each conductor segment can be controlled independently
- Optionally with energy-efficient frequency converter for metered discharge capacity
- Available as "non-trafficable", "trafficable" and "force-reduced", for a particularly small load introduction into the foundations
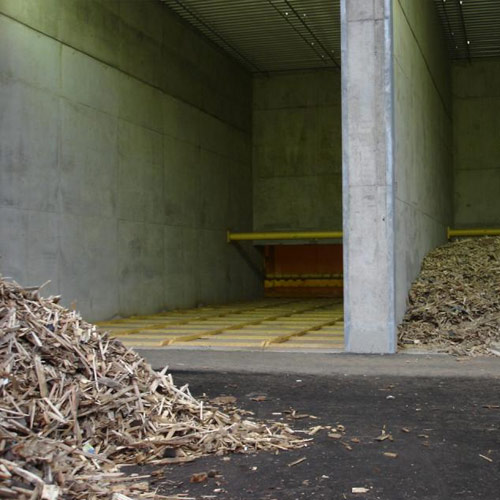
VSB – Hydraulic discharge device (pulling cylinders)
- VSB series hydraulic discharge device is suitable for storing and discharging – even difficult materials
To store and discharge bulk materials such as sawdust, sawdust shavings or wood chips, we provide you with high-performance push rod dischargers. The hydraulically driven push rod dischargers alternately across the floor of the hopper. Pusher floors are suitable both for material intake and for storage with metered discharge.
Your advantages at a glance
- Precise dosing through intelligent control in conjunction with appropriate hydraulics
- Available in different versions - drivable and non-drivable design as well as a deep bunker
- Modular design and therefore universally applicable for many requirements
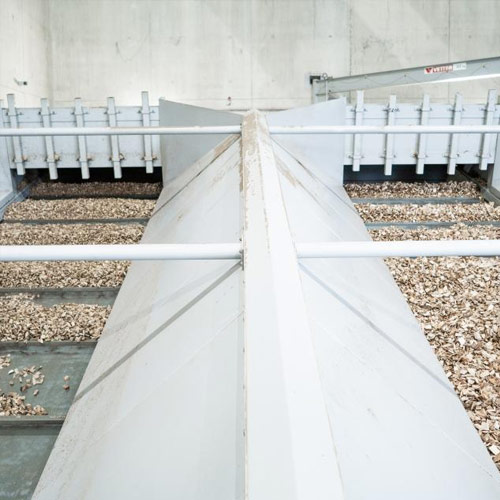
VKB - Drag chain discharger
- Drag chain dischargers are proven systems for the storage and metered discharge of bulk materials
For small storage units up to 100 cubic metres, we offer you efficient systems with our drag chain dischargers. These consist of a steel construction with two lateral conveyor chains. The transverse feed dogs screwed in between move the bulk material stored on an intermediate floor to the discharge side and transfer it perfectly dosed to the downstream conveyor. Low conveying speeds ensure long-lasting operation. You will benefit from our drag chain dischargers in furnace collection containers, for example, or as a discharge device in low-level bunkers. Scraper floors are also often used as truck reception.
Your advantages at a glance
- Feed tank for firing plants or material receiving station
- Low kinetic movement with high discharge capacity
- Flexible use either above ground or in bunkers
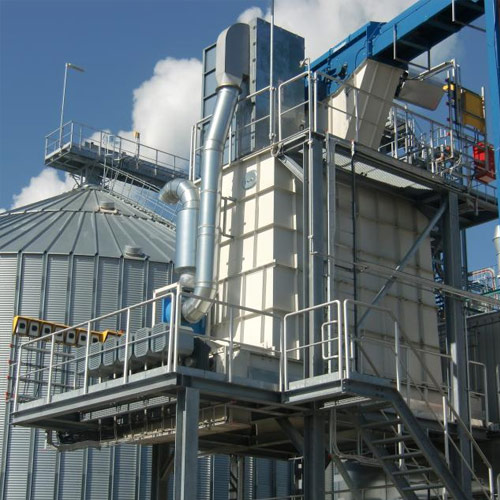
VSM - Screw discharger
- Even difficult goods, such as bark or paper, can be discharged from our multiple screw discharge floors without any problems
Do you need a discharge bin for your bulk material? Then rely on our multiple screw discharge trays, which are also suitable for polygonal silos. The discharge trays consist of modularly assembled screw shafts. Filling volumes and discharge rates can be adjusted by the number and size of the augers. Each screw shaft has a drive unit.
Your advantages at a glance
- Prevention of bridging and segregation of the material
- Versatile use thanks to modular components
- High conveying capacity and even volume flow
- Long lifetime, low maintenance requirements
Seperating
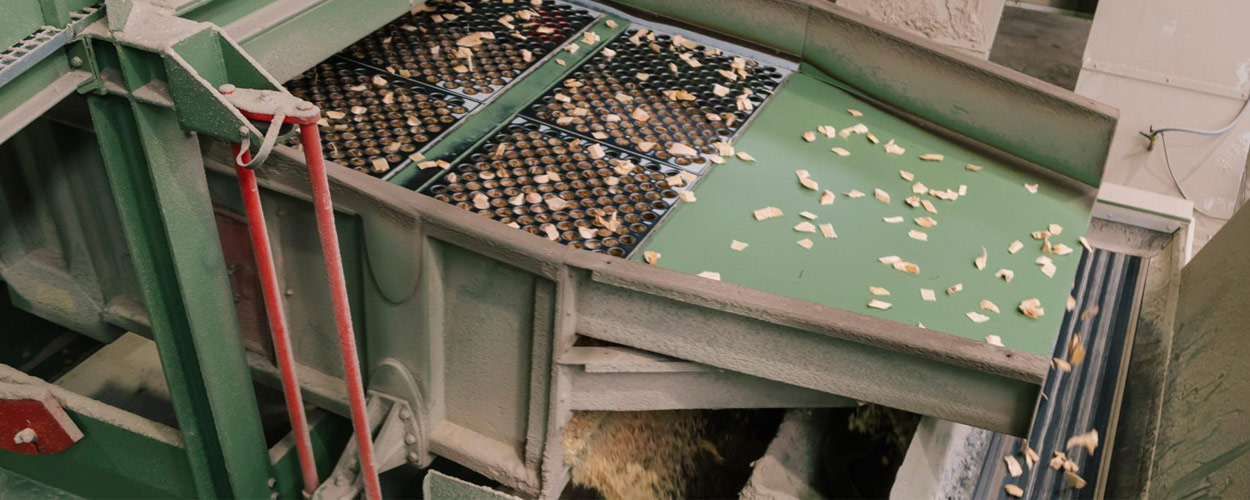
Separation of tramp material guarantees high availability of your equipment
Nach dem Zerkleinern müssen Stör- und Fremdstoffe zuverlässig aus dem Materialstrom heraussortiert werden. Wir bieten unter anderem Systeme, um Eisen- und Nichteisenmetalle aus der Masse zu ziehen und liefern Lösungen, um Leicht- und Schwerfraktionen voneinander zu trennen. Insbesondere in der Aufbereitung von Ersatzbrennstoffen profitieren Sie damit von einer deutlich besseren Output-Qualität. Alle unsere Separierlösungen sind robust, sicher ausgelegt und wartungsarm.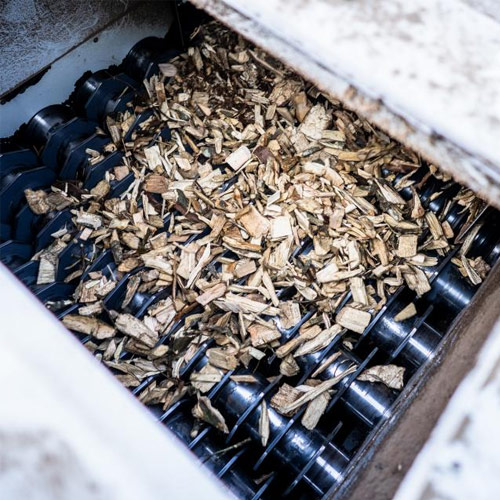
VSR - Disc separator
VST - Star screening machine
- High-performance and flexible screening solution for use in biomass and waste processing
With our disc separators you can separate overlengths from sorted and abrasive material, depending on the design. It can be used for the efficient screening of: Bark, green waste, wood or even dry stabilised material as well as household and commercial waste. Due to the segmental design, the screen length and capacity can be adapted to the specific capacity. The material is optimally fed via a horizontal conveyor belt.
Your advantages at a glance
- High screening capacities with lowest energy consumption, low operating and maintenance costs
- Extremely reliable, hundreds of times in use
- Separation cuts between 30-500 mm can be selected according to task specifications
- Solid sectional steel construction with good accessibility for maintenance and inspection work
- Low maintenance due to automatic lubricators, central lubrication optionally available
- Flexible bearing of the wear-resistant discs to avoid blockades
- Optimally adapted shaft diameter as winding protection
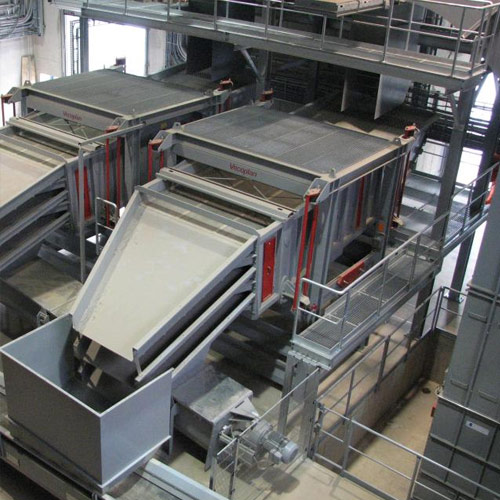
VSS – Oscillation screen
- High-performance vibrating separators ensure optimum particle size separation
With our vibrating separators, you can separate sawmill residues such as wood chips, sawdust, wood shavings, bark or even substitute fuel into different grain sizes very efficiently. Up to 6 fractions can be separated. In particular, fines and overlengths can be screened out of high-quality fractions, thus increasing the value of the middle fractions. Our vibrating sifters consist of inclined circular vibrating screen boxes, which are self-supporting and suspended in a steel frame. The large oscillation range creates an optimal separation effect.
Your advantages at a glance
- optimum cutting result due to acceleration and circulation of the material
- robust industrial design and long service life of all parts
- no product destruction
- subsequent change of fractions possible by changing the screen lining
- simple and quick maintenance, central lubrication optionally possible
- quick screen change device for maximum time saving during screen changes (optional)
- effective screen cleaning (optional)
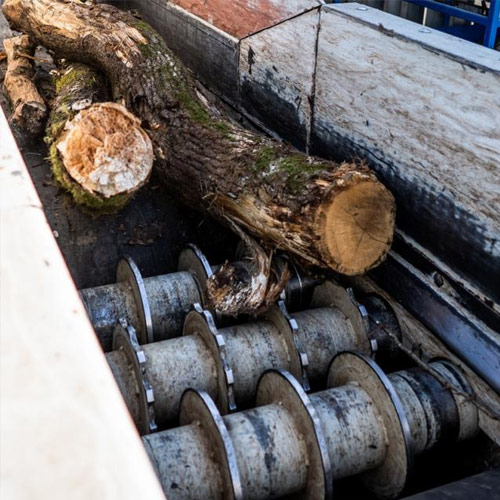
VRA – Roller separator
- Roller separators - optimum protection for your plant
Our VRA series roller separators are available in 2 versions. Roller separators reliably separate pieces of bark and foreign matter such as sand and stones from the feed material or separate excess lengths such as pieces of board from the material flow. This protects the downstream components such as the conveyor system from foreign matter and, in particular, the shredder from wea
Your advantages at a glance
- high availability of the downstream system, protection against faults
- Very compact design
- space-saving installation downstream of a conveyor belt or a vibrating chute as well as in a sheeting between two drag chain conveyors
- robust and easy-to-maintain technology, permanent lubrication optional
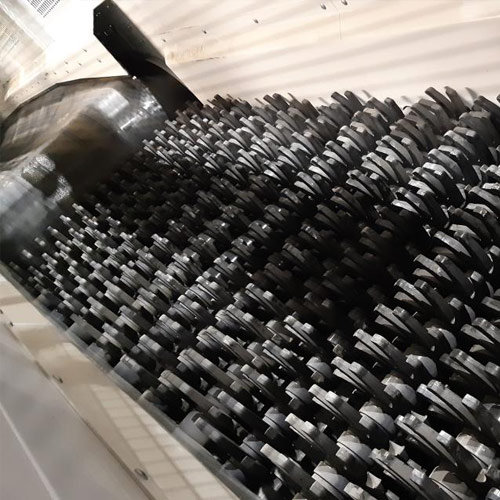
VST - Star screening machine
- High-performance screening of excess lengths
Do you need to screen out excess lengths from your bulk material stream? Our efficient starscreen machines are the answer. These powerful machines are used particularly frequently in sawmills for screening out excess lengths from bark and wood chips. They consist of several horizontal shafts arranged one behind the other and fitted with interlocking screening stars. The rotary motion of the shafts transports the bulk material horizontally. The bulk material falls through the remaining opening between the shafts and screen stars.
Your advantages at a glance
- particularly suitable for screening large volume flows, e.g. wood chips and bark
- high screening capacity with low space requirement
- low energy consumption, no jamming
- low maintenance costs, perma lubrication, optional cental lubrication
Complete installations
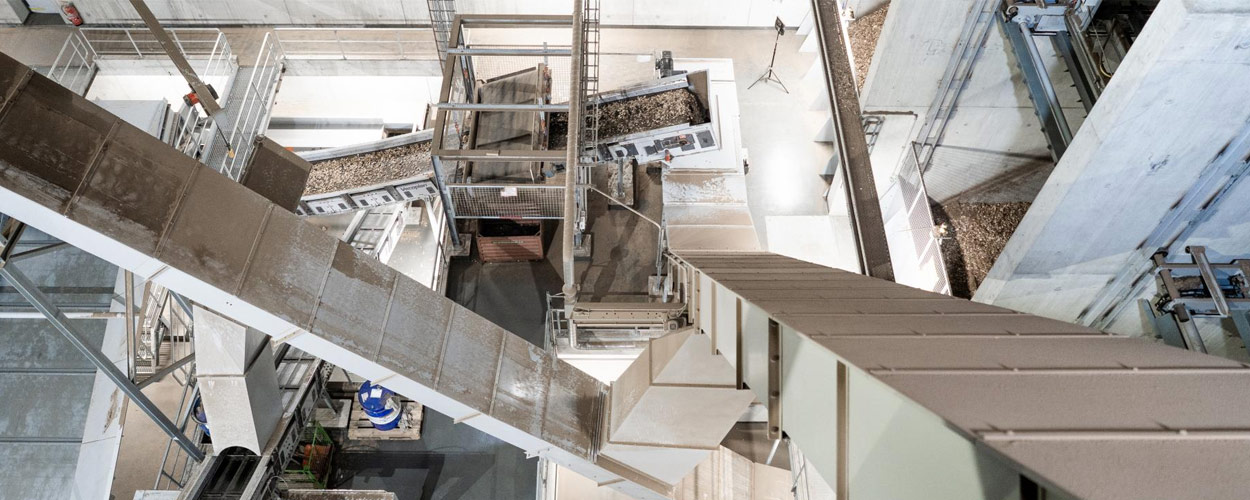
Perfectly designed treatment process
An optimal process chain in the preparation for recycling or thermal recovery always requires coordinated processes and continuous material flows. As a manufacturer of all relevant components, we ensure trouble-free preparation and optimised subsequent handling when designing your plant.
As precise as Swiss clockwork
Only few products stand for precision and reliability as much as Swiss watches. Something that works "as precisely as a Swiss watch" simply works perfectly. One tooth meshes with the next, there is no faltering and no stumbling. Perfect, smooth operation is guaranteed.
We also pursue this goal when designing your systems for complex treatment processes. Here, too, the coordination of the individual items with each other is the basic prerequisite for a successful material flow. Vecoplan is an international expert in mechanical processing and not only offers the strongest individual components from a single source, but has also acquired the know-how over the last 50 years to combine them into a complete installation in line with requirements.Material
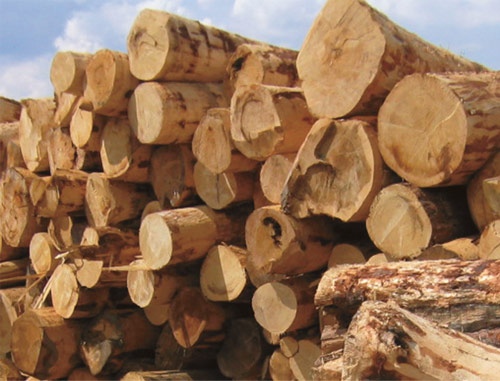
Wood
- Intelligently bring wood residues that accumulate in sawmills, joineries or during furniture production into the residual material cycle.
Processing wood leftovers instead of disposing of them, then using the output thermally or as a raw material is an economically attractive option for sawmills, joineries and furniture manufacturers. We supply the right technology to help you achieve this. Our shredding and processing technologies are an integral part of the wood, raw and residual materials cycle. We can deliver the entire material preparation process to you. Our plants shred the materials into a high-quality, homogeneous output material. We also have transport solutions for a dosed supply and for safe storage.
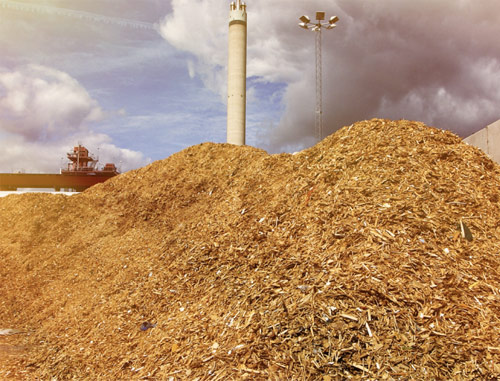
Biomass
- Technologies and machines in biomass processing for reliable supply of biomass heat and power plants
Biomass CHP plants, also known as biomass cogeneration plants, generate electrical energy from biogenic solids, plus a great amount of additional heat that can be used efficiently. To ensure a smooth combustion process, the mass must first be mechanically prepared in advance to obtain a homogeneous unit that is free of impurities. We also supply equipment that stores, doses and conveys the various materials. You’ll get a Vecoplan system for the individual feeding and preparation of the fuels, and it will be perfectly tailored to match your usage scenario.
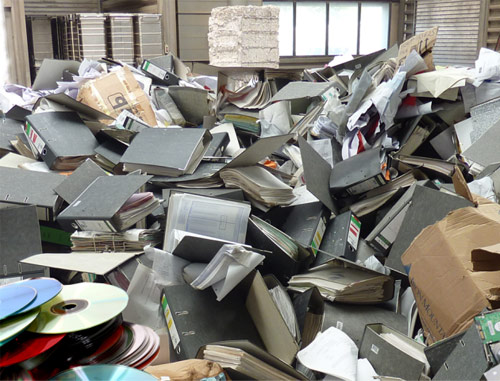
Files and Data storage media
- Security in the destruction of files and data
Benefit from consistent safety, maximum shredding performance, end-to-end plant efficiency and overall cost-effectiveness that pays off for you.
Highly secure and efficient shredding of files and data media
TÜV-certified security levels, according to DIN 66399-2
Realisation of complete plant systems according to DIN 66399-3
Our engineers are specialists in their field. The result is particularly powerful document destruction and data media shredders that have been security requirements down to the last detail.
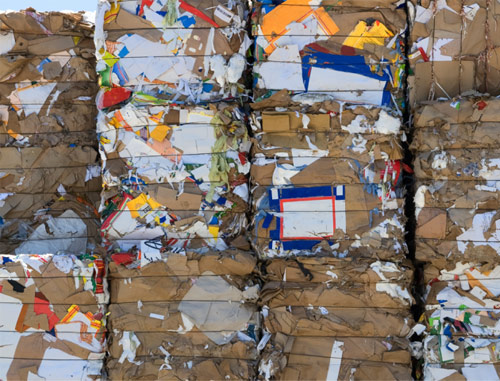
Paper and pulp
- Shredding of paper waste from production or recycling operations in preparation for return to the recyclable material cycle
We offer shredding solutions that economically and efficiently return waste paper, paper rolls or bales, production rejects and cardboard to the recycling loop. If you are responsible for the preparation of these materials in paper production, paper processing or recycling, we will provide you with solutions that are exactly tailored to your requirements and your input materials.
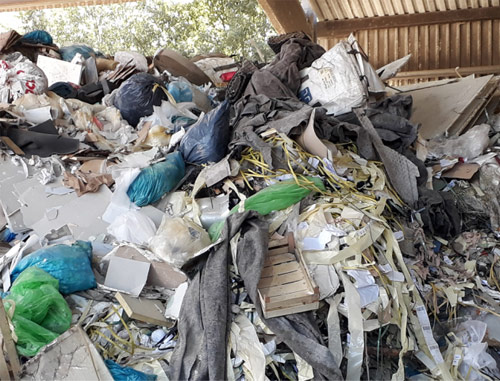
Domestic and industrial waste
- The processing of often problematic waste requires well thought-out solutions for sustainable treatment
Do you want to process waste efficiently and return it to the materials cycle? We supply complete processing plants for this purpose. With our solutions, you can pick up various materials after delivery, store them, free them from impurities, shred them into a high-quality output and transport them. To achieve all of this, we can supply you with a range of machines, including powerful pre- and post-shredders, metal separators, conveyor belts and screening & separating units. Step-by-step, the material flow is separated into its various fractions and processed as required. You’ll benefit from coordinated systems with high levels of availability and economic efficiency.
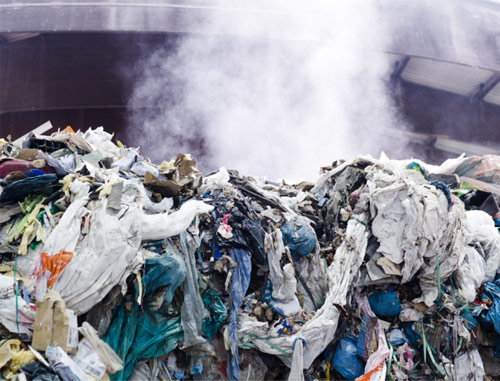
Alternative fuels
- Planning and implementation of complete processing plants in refuse derived fuel production
In order to reduce the costs involved in the energy-intensive production of cement, many manufacturers are turning to refuse-derived fuels (RDF), considerably reducing the proportion of expensive primary fuels they would normally use. Solid fuels are being increasingly used – these might be used tyres, waste wood or mixtures of plastics, paper, composite materials and textiles. Vecoplan provides operators of cement plants with proven and robust components for conveying the material and separating iron and impurities, efficient receiving stations, storage systems and, of course, efficient shredders for an output in various qualities.
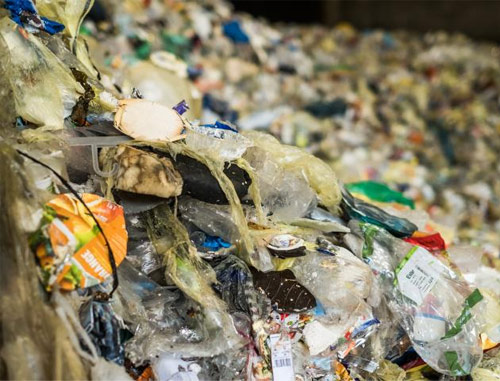
Plastics - post consumer
- Waste from the use and consumption of plastic products generated by private or commercial end users
The reduction and recycling of plastics are recognisably in the political and European focus. The European Strategy for Plastics in the Circular Economy, the German Resource Efficiency Programme III and the new EU Action Plan for the Circular Economy; they all define measures for the use of plastic recyclates and for increasing the production and procurement of plastic products from post-consumer recyclates (PCR).
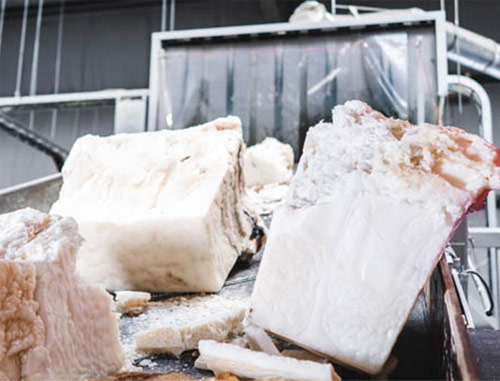
Plastics - post industrial
- Waste generated during the manufacture of plastic products in industry. The high-quality and valuable raw materials can be processed and returned to production as recyclate
Post-industrial recycling materials such as purgings, lumps, semi-finished plastic products, films and production & process waste are particularly challenging. We will supply you with powerful solutions for efficient processing into high-quality output. Our systems will efficiently shred, convey, dose and safely store your different materials. We’ll develop the right processing strategy together with you in our Technology Centre.
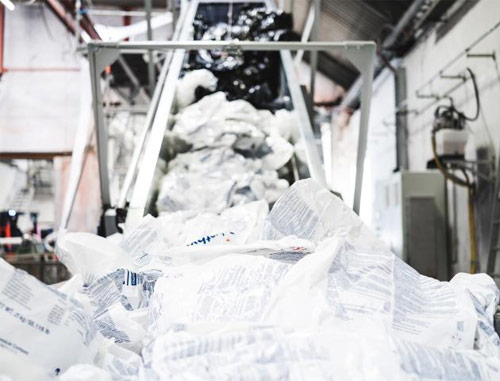
Plastics - in-house recycling
- In in-house recycling, plastic waste that is a by-product of production is directly processed in a closed loop and fed back into production as raw materials
Would you like to process your reject material into regranulate so that it can be re-introduced into production? In-house recycling has become an established practice, because processors make significant cost savings by using this procedure. On the one hand, they have to pay less for expensive new material and on the other, there’s no need for disposal in external recycling plants. Vecoplan will supply you with exactly the right machines for efficient and high-quality output. We have installed machines that are suitable for processing many materials in our Technology Centre, so we can test the individual materials you need in your applications and develop processing strategies that will match your requirements perfectly.